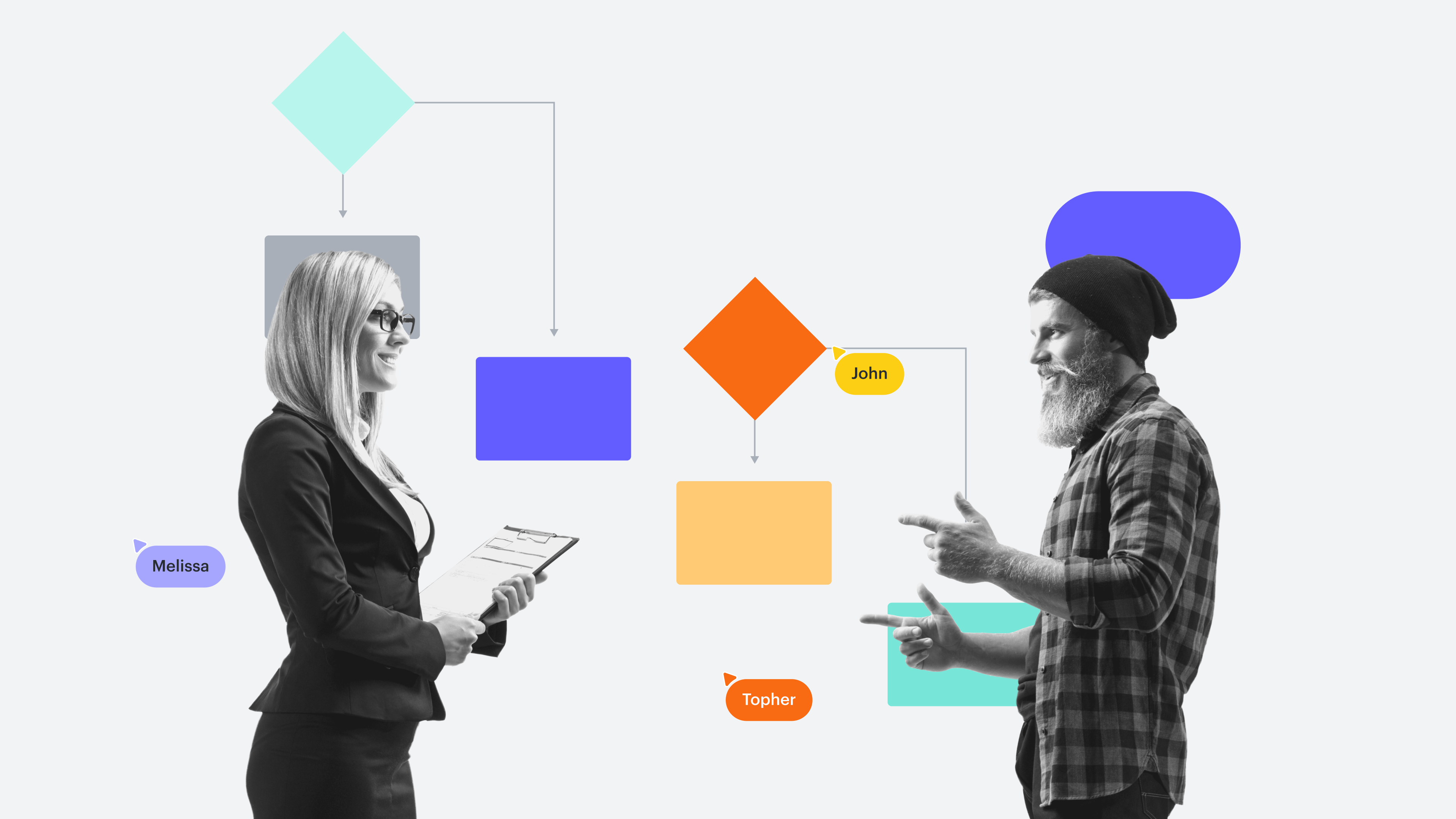
How to apply the Theory of Constraints within your business
Lucid Content
Reading time: about 7 min
Topics:
5 steps in the Theory of Constraints
- Identify the constraint
- Exploit the constraint
- Subordinate and synchronize to the constraint
- Elevate the performance of the constraint
- Repeat the process
In 1984, an Israeli businessman named Eliyahu M. Goldratt wrote a novel called The Goal: A Process of Ongoing Improvement to introduce a management methodology he called the Theory of Constraints. Goldratt’s novel centers around a manager who oversees a manufacturing plant that has three months to turn things around or it will be shut down.
With the help of an acquaintance, the manager recognizes that there will always be constraints in manufacturing—and that the key is to identify and address those constraints early.
Many businesses around the world have adopted this methodology to better understand the factors that could be keeping them from their goals. Learn more about the five steps of the Theory of Constraints and see what tools you can use to optimize your processes.
What is the Theory of Constraints?
Goldratt’s Theory of Constraints is a process improvement methodology that recognizes that there will always be at least one factor that will constrain processes or manufacturing.
Theory of Constraints: 5 steps
The following five steps of the Theory of Constraints are designed to help you discover constraints early in order to minimize or eliminate them.
-
Identify the constraint: Identify the specific part of a process that is keeping you from meeting desired goals. Constraints can come from internal factors, such as lack of training or poorly designed processes, or external factors, such as a shortage of materials.
-
Exploit the constraint: Determine how you can use existing resources to reduce the constraint's impact. For example, if the constraint is an overworked employee, redistribute assignments to get the work done.
-
Subordinate and synchronize to the constraint: The parts of the process that are not constraints need to align with and support the constraint. For example, a construction worker can only use one tool at a time. You wouldn’t keep trying to hand him wrenches or screwdrivers while he is using a hammer.
-
Elevate the performance of the constraint: If the constraint still exists, you will need to make it a higher priority. For example, you may need to hire more people to increase the workflow in the area where the constraint exists.
-
Repeat the process as needed: The Theory of Constraints is an ongoing process that allows you to continually find ways to improve. You will need to repeat these steps to ensure that you are getting the work done and meeting goals.
Benefits of using the Theory of Constraints
Much like other management processes such as Lean manufacturing and Six Sigma, the Theory of Constraints keeps you focused on what needs to be improved so you can eliminate the things that impede progress and don’t work.
Following the five steps of the theory of Constraints can lead to:
- Increased profit
- Faster process improvement
- Capacity to manufacture more products
- Reduced lead times
- Reduced inventory
Ready to take advantage of these benefits? While Lean manufacturing has a slightly different focus than the Theory of Constraints, many of the tools used to eliminate waste and reduce costs within Lean can be repurposed to identify and eliminate constraints.
Lean tools for identifying the constraint
Value stream mapping
A value stream map gives you and your team a visual overview of every step it takes to create a product or service. By tracking people, procedures, information, and inventory, your team can identify the non-value added areas where constraints may impede your processes.
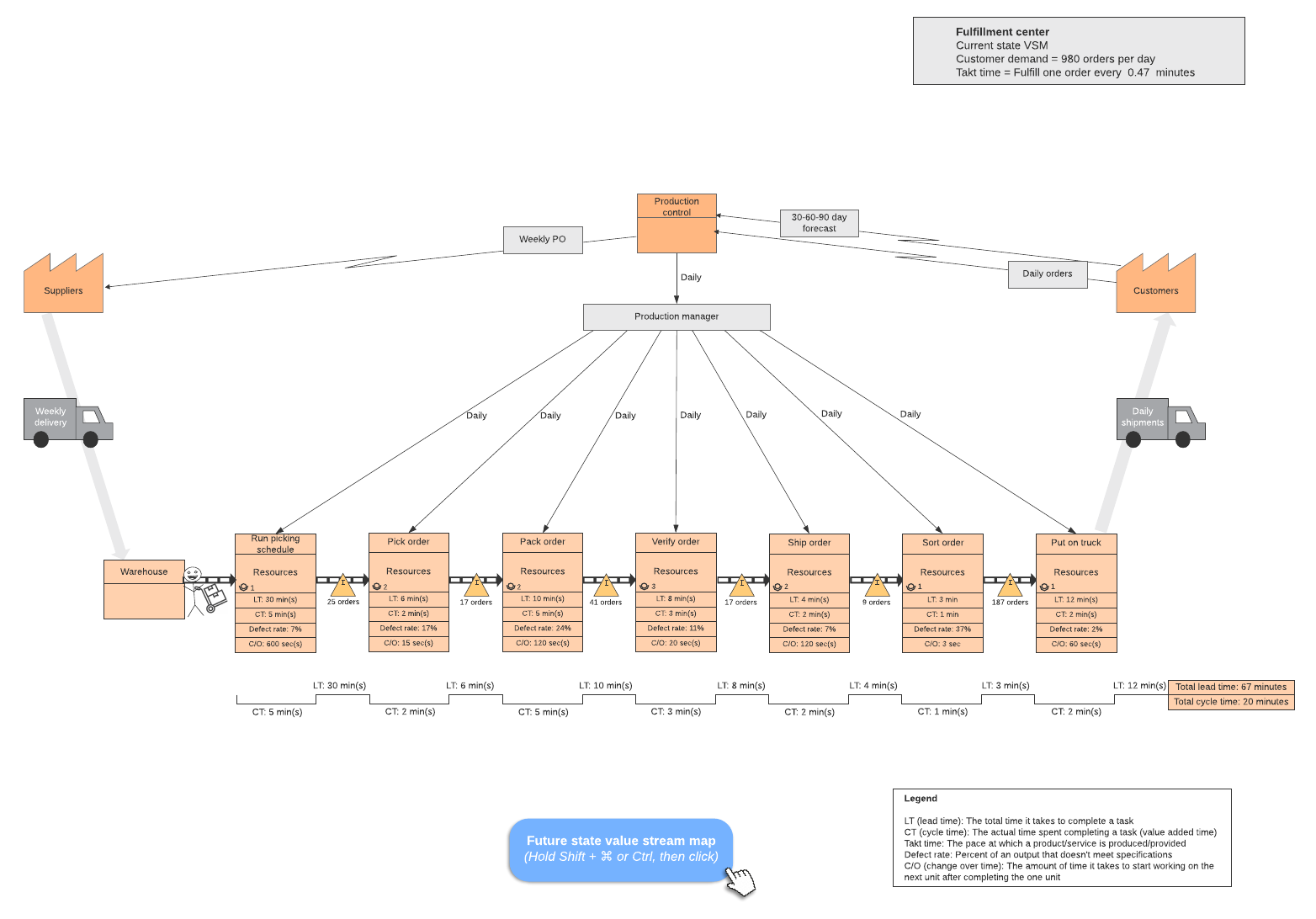
5 Whys analysis
Like a weed in a garden, a problem will continue to come back unless you can dig down and eliminate its root. Developed by Sakichi Toyoda, the five whys analysis will help you find the root of a problem by asking “Why?” five times.
A fishbone diagram is a similar tool that can help you through root cause analysis as you examine potential causes in multiple categories.
Lean tools for exploiting the constraint
Kaizen
Kaizen is a Japanese word meaning “change for better” and is based on the belief that everything can be improved. More of a philosophy than a tool, the Kaizen methodology looks for the most efficient way to perform processes and complete tasks. After identifying a constraint, Kaizen requires everybody involved from the top down to find and suggest ways to improve the process to reduce the constraint’s impact.
5S
5S is used to create organized, safe, clean, and efficient work environments. It keeps processes flowing and minimizes the impact of constraints. The 5S steps include:
- Sort: Sort through inventory and eliminate non-essential items to reduce the time to find what you need.
- Straighten: Organize your inventory and tools so they are easily accessible.
- Shine: Clean the work area and keep it organized.
- Standardize: Make the process of sorting, organizing, and cleaning a standard.
- Sustain: Keep following this process and make sure employees stick to it.
Andon
Andon has its roots in the Toyota Production System. On the Toyota manufacturing floor, an operator could pull a cord above the line to halt production at the first sign of trouble. Andon enables team members to stop work and immediately come together to solve a problem in real time. It increases process transparency, drives efficiency, decreases waste, and empowers team members to own the process and take immediate action.
Standardized work
Standardized work is central to Lean manufacturing. It takes improvements resulting from the Kaizen process and turns them into standardized workflows. Think of it like a playbook. Your team decides the best way to get something done and that process becomes the current standard. If you’re implementing standardized work, you should be able to answer three questions:
- Do all team members know exactly what to do and how to do it?
- Can team leaders quickly and accurately verify that team members are working according to standard processes?
- Do team leaders know what to do if they observe that standards aren’t being followed?
Standardized workflows lead to personal accountability, team-wide discipline, and continuous improvement.
Lean tools for subordinating the constraint
Kanban
As a management tool, the Kanban methodology uses visual signals—cards on a board—to track work to be done, work in progress, and finished work. Kanban contributes to this step in the Theory of Constraints because it is designed to manage the workflow—you can’t start on the next task (the subordinate) until the current task (the constraint) is completed.
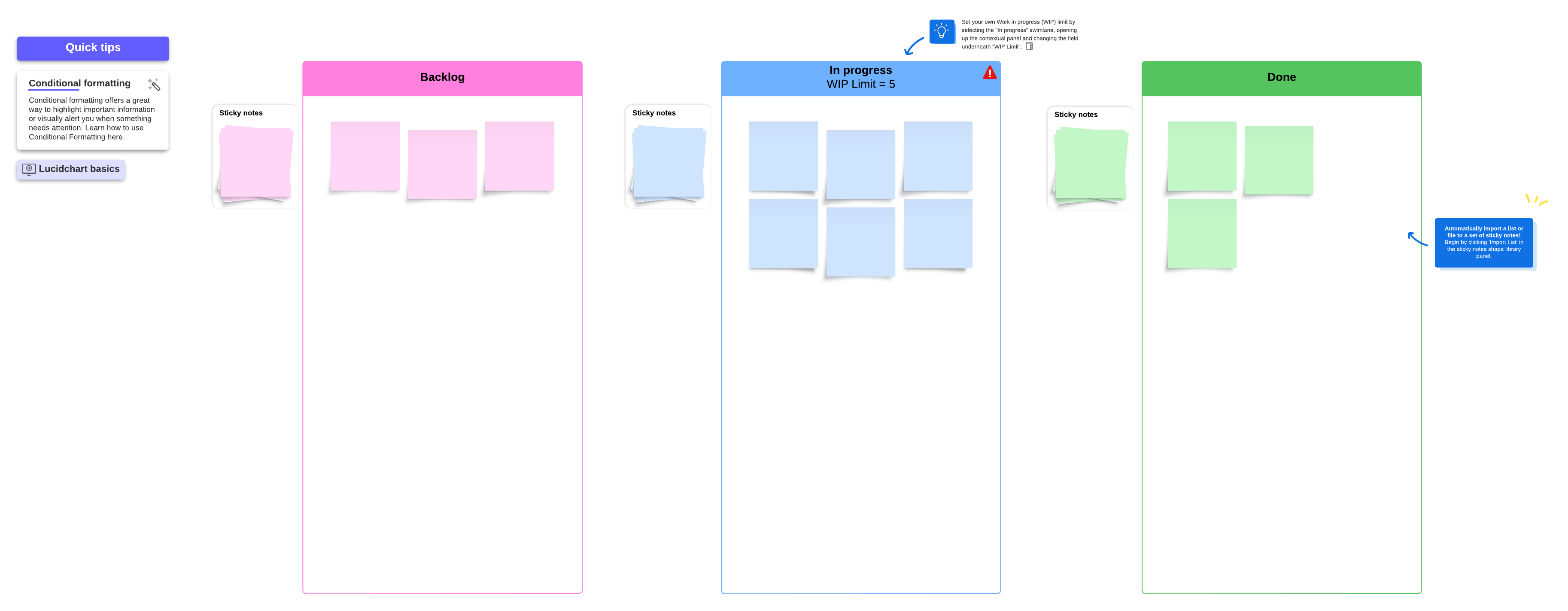
Drum-buffer-rope
Also created by Eliyahu Goldratt, the drum-buffer-rope method constraints the amount of work in progress. Every system has a bottleneck, referred to as the drum. The drum dictates the throughout, or the amount of work that can be completed. The buffer refers to the work waiting to pass through the bottleneck. If this buffer is ever maximized to 100%, the bottleneck becomes overloaded. The buffer should release the right amount of work (the rope) to keep the bottleneck operating at optimal levels.
Drum-buffer rope is specifically designed to manage constraints by focusing on the parts of a process that are not bottlenecks. It dictates when these parts of the process should speed up, slow down, or stop.
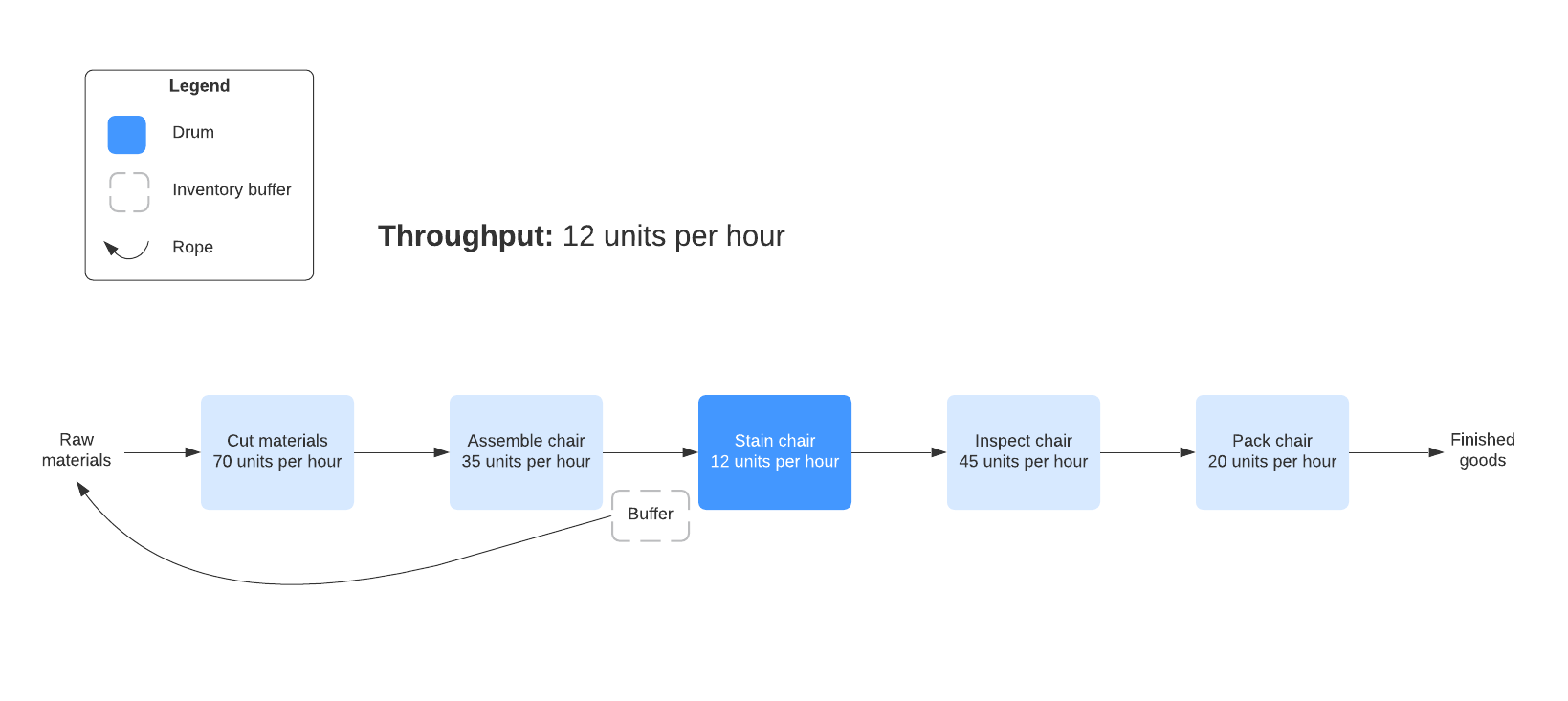
Lean tools for elevating the constraint
Total Productive Maintenance (TPM)
The idea behind Total Productive Maintenance (TPM) is to get employees involved in maintaining their own equipment with an emphasis on proactive and preventative measures in an effort to achieve zero breakdowns, zero small stops, zero defects, and zero accidents.
Poka-yoke
This Japanese term means “error prevention.” It is used during the production process to define, measure, analyze, improve, and control defects during the production process. The goal is to reduce the need to go back and redo the work later. Applying poka-yoke to the Theory of Constraints can help to maximize the throughput of bottlenecks because the improvements you make during the process are designed to prevent further errors.
These are just a few of the management tools that can be integrated and used with the Theory of Constraints. Visit the resources above to learn more about these Lean tools and begin using them with customizable Lucidchart templates.
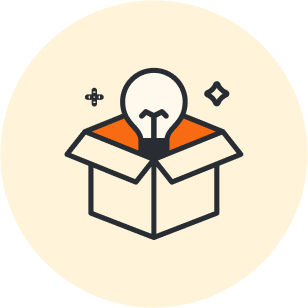
Learn about the best tools for lean process improvement and start using them today.
Learn moreAbout Lucidchart
Lucidchart, a cloud-based intelligent diagramming application, is a core component of Lucid Software's Visual Collaboration Suite. This intuitive, cloud-based solution empowers teams to collaborate in real-time to build flowcharts, mockups, UML diagrams, customer journey maps, and more. Lucidchart propels teams forward to build the future faster. Lucid is proud to serve top businesses around the world, including customers such as Google, GE, and NBC Universal, and 99% of the Fortune 500. Lucid partners with industry leaders, including Google, Atlassian, and Microsoft. Since its founding, Lucid has received numerous awards for its products, business, and workplace culture. For more information, visit lucidchart.com.
Related articles
How to conduct a 5 whys analysis
Stumped on a business problem? Try using the 5 Whys. By urging you to look deeper into the issue, the 5 Whys analysis can help you discover the root cause of a problem and put you on track to fix it.
Single-Minute Exchange of Dies: Improving lean operations
Keep reading to discover what SMED is, why it is beneficial, and how to use the SMED process to improve operations within your organization.
Lean methodology 101
In this article, we’ll discuss how the Lean methodology can help you to improve productivity, eliminate waste, and keep your customers happy.