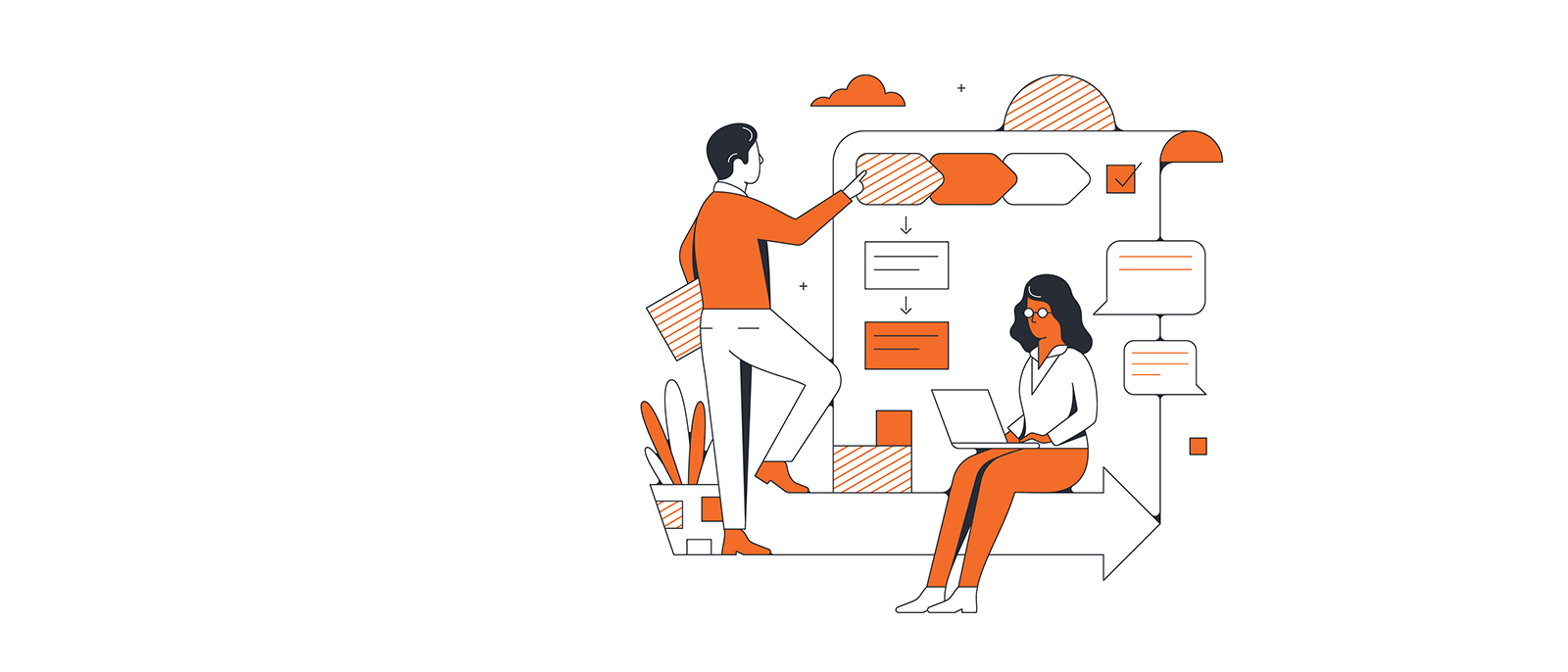
Overview of poka-yoke in Lean manufacturing
Reading time: about 8 min
Poka-yoke (pronounced PO-kah yo-KAY) is a Japanese cartoon, it’s actually a Japanese term that means to avoid (yokeru) mistakes (poka).
Poka-yoke is one of several Lean manufacturing tools designed to help organizations eliminate waste, streamline processes, and increase efficiency. Specifically, poka-yoke tries to achieve zero defects by preventing and eliminating errors.
Often referred to as “error-proofing” or “mistake-proofing,” the idea of poka-yoke was developed in the 1960s by Shigeo Shingo, a Japanese industrial engineer whose production innovations are still important in Lean and Six Sigma methodologies today.
In this article, we will:
- Define poka-yoke and briefly explore its history.
- Discuss how poka-yoke fits into Lean manufacturing.
- Present some poka-yoke examples.
- Show you how to implement the poka-yoke system in your organization.
What is poka-yoke?
While visiting a plant in the early 1960s, Shingo noticed that workers were forgetting to insert springs in a simple on/off switch. This one small mistake resulted in defective parts being manufactured and shipped. From his observations, Shingo learned two things:
- Sometimes people forget to do things.
- Sometimes people forget that they have forgotten to do things.
Knowing that these simple human errors were the root cause of the problem, Shingo started working on ways to improve the process and to make it “idiot-proof” (baka-yoke). After a worker complained that the term was insulting, he changed it to poka-yoke, which shifts the focus from the worker to the process.
By redesigning the process so that the operation could not proceed until the worker had inserted the spring into the switch, fewer human errors were made and higher quality products were shipped.
You encounter poka-yoke every day. For example, you can’t start the microwave until the door is closed, and it will stop immediately if you open the door before the timer has stopped. In addition, you often create your own poke-yoke by doing something as simple as taping your car keys to an item that you need to take to work.
How does poka-yoke fit into Lean manufacturing?
The main purpose of Lean is to eliminate waste, continually improve processes, increase product value, and solve customer problems all while reducing your costs. Lean concepts and tools are generally simple and easy to implement. For any Lean implementation to be truly successful, you must have total buy-in of all employees from the top down.
As with the Lean concept of the Theory of Constraints (TOC), poka-yoke recognizes that there will be constraining factors that can slow down manufacturing and result in defective products. Your job is to find the root causes of the constraints.
After identifying the root cause, TOC aims to exploit the constraint using existing resources to reduce the impact of the constraint. For example, if the constraint is an overworked employee, redistributing assignments to balance the workload can lead to increased efficiency and higher productivity.
Poka-yoke complements TOC by implementing processes or fixes that make it impossible for constraints to exist in the system. For example, it’s impossible to start an automatic car if the selection lever is not set on Park. This makes it impossible for the car to accidentally move when you turn the key, eliminating the possibility of making a mistake.
Types of poka-yoke
There are two types of poka-yoke: control and warning.
- Control: The goal is to make it mechanically impossible to make mistakes. For example, there is only one way you can plug a three-prong electric cord into a power outlet.
- Warning: Color or sound is used to alert operators that they are about to make a mistake. For example, a message pops up on your screen to remind you to save your documents before closing an application.
The goal of any poka-yoke system should be zero defects. Let’s say that you only have one defect out of every 10,000 units produced. That’s a very good ratio. However, that one defect represents a 100% defective product to the person who buys it.
Benefits of using poka-yoke
Implementing poka-yoke in your organization will benefit your organization in many ways:
- Error prevention (control) and error avoidance (warning) means that you spend less time and money training your employees.
- Fewer errors means more safety for workers and consumers.
- Less time and money is wasted on quality checks and inspection because the system is designed to be mistake-proof.
- Employees adopt a culture of continuous improvement as a way of life.
- Zero defects, or as close to zero as possible, reduces waste and costs.
- Higher quality products lead to increased customer satisfaction and stakeholder confidence.
Using poka-yoke prevents or greatly reduces errors and this builds confidence in employees, management, and stakeholders. Increased confidence that comes from getting work done right the first time can result in superior products, better customer satisfaction, enhanced brand loyalty, and increased profits.
How to implement poka-yoke
Implementing poka-yoke should be easy, inexpensive, and aligned with current processes. You should see immediate benefits and measurable improvements in quality and production. You can implement poka-yoke by using the steps described below.
Step 1: Identify the problem
Remember that humans make mistakes. One or two mistakes are to be expected. A series or pattern of mistakes indicates that there is a problem that needs to be addressed. That problem may be with the employee or with a flaw in a machine.
You’ll need to observe the process to identify where the problem is occurring. Enlist the help of others to determine whether the error is human or mechanical. Consider using a flowchart to visualize your current process and design the future state you want to see.
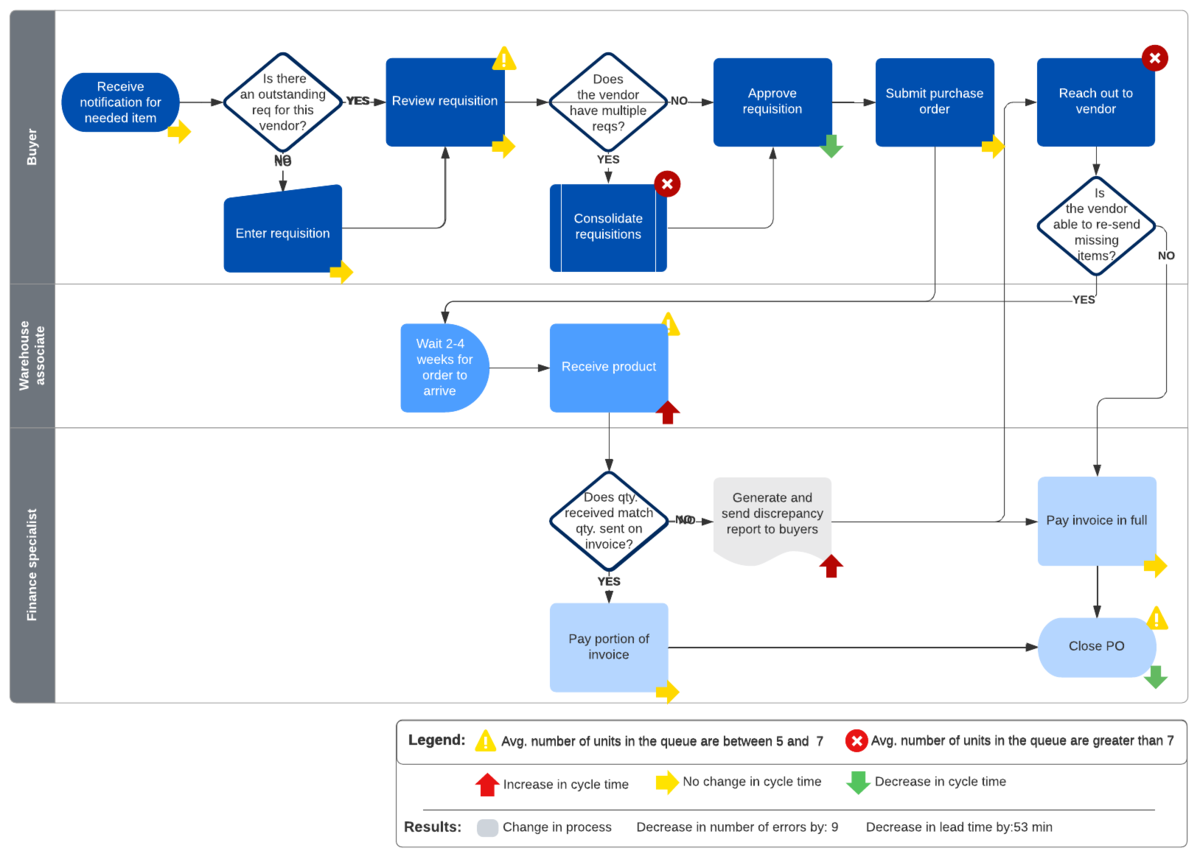
Step 2: Find the root cause
After you identify the problem, determine what is the most likely cause of that problem. You may want to consider using the 5 Whys, another quality control technique developed in Japan, to help you find the root cause. By asking and answering five “why” questions, you will dig down to find the root cause of the problem.
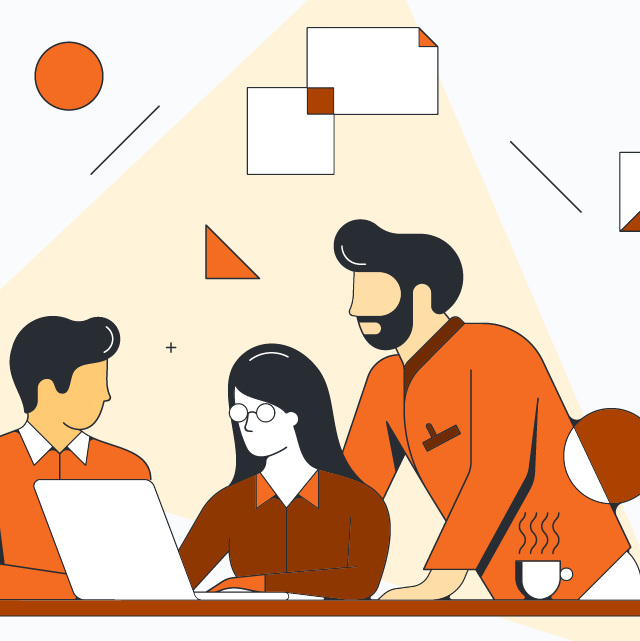
Learn how to complete a root cause analysis—and get started with templates.
Learn moreStep 3: Determine which type of poka-yoke to use
If you can easily prevent mistakes from happening, install a control poka-yoke that prevents the process from continuing until a vital step is completed. For example, the shape of a component ensures that it can only be inserted in the proper way.
If you can’t prevent a mistake, install a warning poka-yoke that alerts the operator that attention is needed before the process can continue. These warnings can include colors, flashing lights, buzzers, or any type of alerts that tell the employee that something needs to happen before the process continues.
Step 4: Determine the most appropriate poka-yoke method to use
There are three poka-yoke methodologies you can choose from.
- Contact: This method uses shape, size, or other physical attributes to identify errors. For example, you can’t insert a square peg into a round hole.
- Constant number: With this method, errors are triggered if a specific number of actions are not made. The operator is alerted if the wrong number of moves are made.
- Sequence: This method ensures that the proper sequence of events is followed before a process can continue. For example, a checklist that has to be completed before production can move to the next step.
Step 5: Test your poka-yoke system to see if it works
Before you can fully implement a poka-yoke, you need to be sure that it will work. Test it to see if the error is prevented and to make sure that the fix does not slow down the process.
Step 6: Train employees
Even the simplest poka-yoke can’t be successfully implemented until employees are trained how to do it. Training helps with employee adoption of the new process, especially if they can see that the fix makes their job easier to do. Add your new poka-yoke to your standard operating procedures (SOP) guide to help employees understand what is expected of them.
Step 7: Review performance and measure success
Observe the operation again and measure success. Begin looking for other errors that may be impeding your production and look for ways to continually improve.
Poka-yoke examples
The following are a few examples of how poka-yoke is used in different industries.
Poka-yoke in healthcare
Mistakes in healthcare can result in further injury and even death. Hospitals and clinics have implemented simple poka-yoke systems with checklists and a series of questions and answers. The next time you go to the hospital, notice how many different times they ask you the same questions (“What is your full name?” “What is your birthday?” “What is your address?”).
It may be annoying to have to answer these questions over and over again, but the system is in place to keep doctors from removing a kidney from the wrong person or operating on the wrong limb.
Poka-yoke in manufacturing
Workshops include a variety of protective error-proofing devices to keep employees safe. For example, workshops have barriers that ensure enough space between the operator and the machine, automatic cutoff switches, and warning signals that are activated when procedures are not followed correctly.
Poka-yoke in the service industry
Think about the last time you paid cash for your meal at a fast-food restaurant. Chances are, your change was automatically dispensed by the cash register. This automated task eliminates the possibility that the cashier might give you the wrong amount of change. Poka-yoke in action.
Poka-yoke is a simple and powerful quality control tool that can be used in any industry to reduce or eliminate errors. Benefits of implementing poka-yoke include saved time and resources by getting work done correctly the first time, better-quality products and services, and increased confidence in your brand and products.
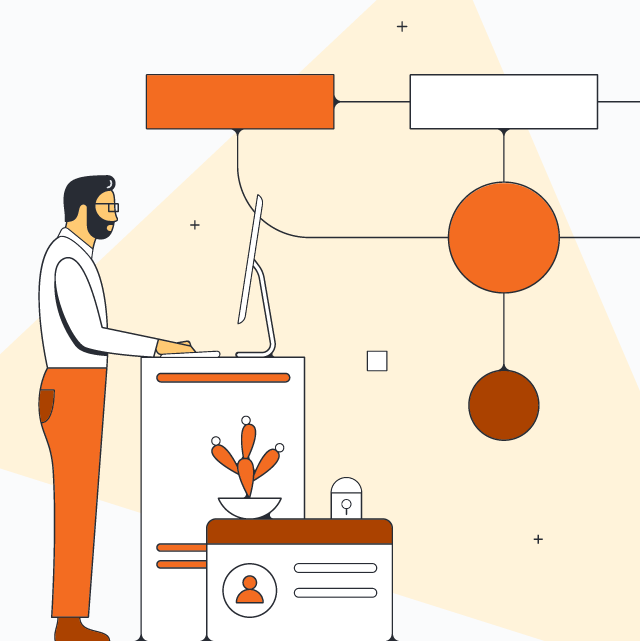
Improve and scale your business processes with Lucidchart.
Learn moreAbout Lucidchart
Lucidchart, a cloud-based intelligent diagramming application, is a core component of Lucid Software's Visual Collaboration Suite. This intuitive, cloud-based solution empowers teams to collaborate in real-time to build flowcharts, mockups, UML diagrams, customer journey maps, and more. Lucidchart propels teams forward to build the future faster. Lucid is proud to serve top businesses around the world, including customers such as Google, GE, and NBC Universal, and 99% of the Fortune 500. Lucid partners with industry leaders, including Google, Atlassian, and Microsoft. Since its founding, Lucid has received numerous awards for its products, business, and workplace culture. For more information, visit lucidchart.com.
Related articles
Setting up standardized work and Lean manufacturing
Learn what the standardized work principle is, plus how documenting the procedures and ensuring that your employees are sufficiently trained will help your operations run smoothly and efficiently.
Single-Minute Exchange of Dies: Improving lean operations
Keep reading to discover what SMED is, why it is beneficial, and how to use the SMED process to improve operations within your organization.