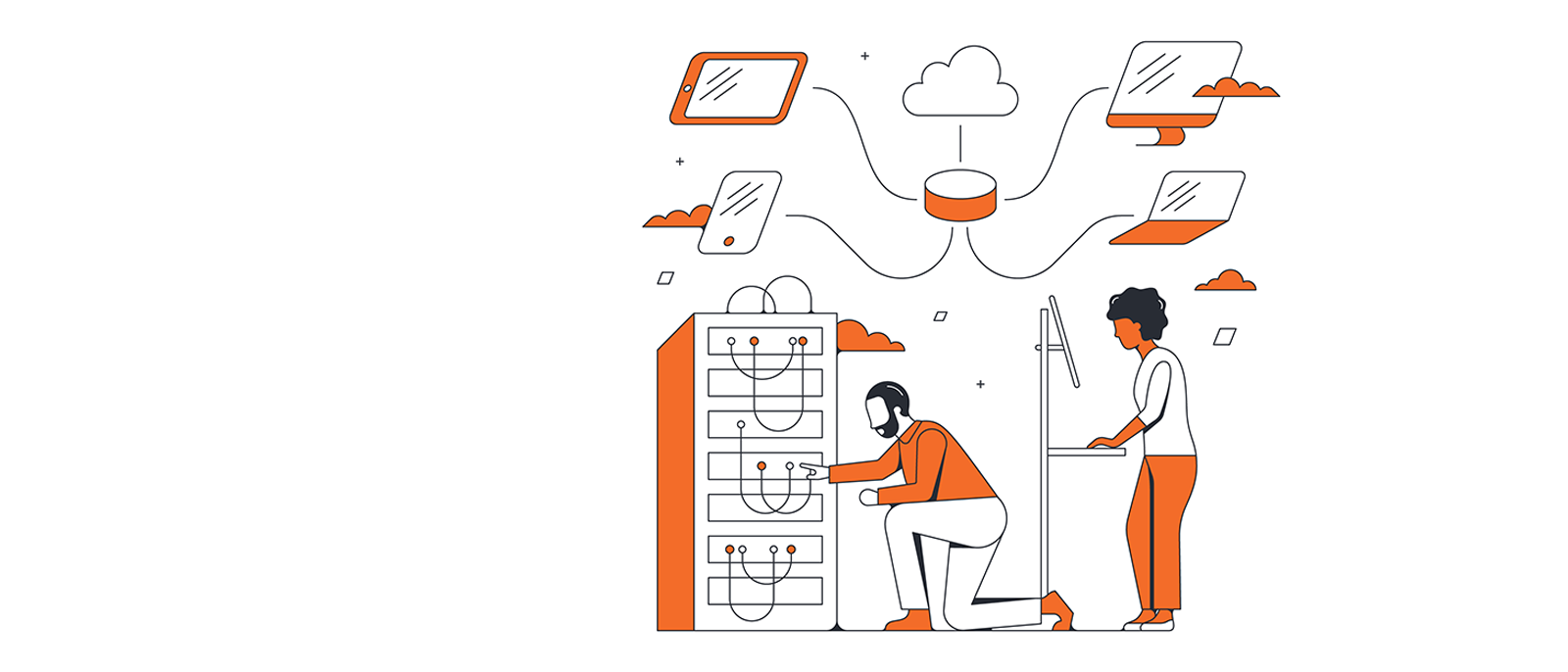
Single-Minute Exchange of Dies: Improving lean operations
Reading time: about 5 min
Topics:
Simplicity, efficiency, and consistency. Many companies turn to Lean manufacturing to improve customer satisfaction while minimizing resources. SMED (Single-Minute Exchange of Dies) is a system used as part of Lean manufacturing to reduce the time it takes to complete equipment changeovers.
Keep reading to discover what SMED is, why it is beneficial, and how to use the SMED process to improve operations within your organization.
What is SMED?
One way to minimize resources is by reducing equipment changeover times through SMED. The SMED process identifies elements as either internal (processes that can only be completed when equipment is stopped) or external elements (processes that can be completed during machine operation).
The SMED technique simplifies the steps in your manufacturing process so that machine changeover time can be completed in less than 10 minutes. Steps are converted into external, and the remaining steps (the internal) are streamlined.
SMED was officially developed by Japanese industrial engineer Shigeo Shingo who moved to the United States to become a Lean manufacturing consultant. Shingo's SMED process reduced changeover times by an average of 94% across multiple industries.
To put that into perspective, that’s like going from a 90-minute changeover to one that is less than five minutes! Shingo’s SMED process opened up more opportunities for manufacturers to increase profit and customer satisfaction.
Why SMED is beneficial
Implementing the technique can yield many benefits for manufacturers, including:
- Lower manufacturing costs: Faster changeovers mean less equipment downtime
- Smaller lot sizes: More efficient changeovers enable companies to have more frequent product changes
- Smaller finished goods inventory: Processes are optimized so that products aren’t sitting in the warehouse for too long
- Improved responsiveness to customer demand: Smaller lot sizes enable more flexibility in scheduling
- Improved equipment startups: More consistent, streamlined flow
Often, the SMED technique helps to uncover areas where improvement is needed within the operations process.
Implementing SMED
According to Vorne, a manufacturing solutions company, these are the necessary steps for integrating the SMED manufacturing process into your organization:
- Establish a pilot area
Observe and record a process in the company and how long it takes for changeover to complete. This becomes your baseline that you will work to improve.
- Identify internal and external elements
After determining the pilot area, determine the classification of the elements. One way to effectively do this is by filming an entire system changeover process and then analyzing it with your team. Clearly label each element (as internal or external), and give a detailed description of each.
It is important to be mindful of a couple of things:
- Most changeovers have about 30-50 elements
- Record both human and equipment elements (this will help with optimizing later)
- Separate external elements
Review each element from the previous step and ask yourself if the element can be performed while the machine is operating. Be sure to have a solid understanding of your external elements.
Once you complete this step, you should have a thorough list of both internal and external elements.
- Convert internal to external
Review the internal elements—is there a way to make them external? If so, how? After this assessment of each internal element, prioritize them. List them in order from most promising results to least.
Consider the following techniques to convert internal elements to external:
- Prepare in advance: Preparing parts in advance and keeping them in a ready-to-go status can cut a significant amount of time.
- Make adjustments before the changeover: Consider using duplicate jigs for performing alignment and other adjustments before the changeover process begins.
- Equipment modification: Modify equipment to make it safer to perform tasks (like cleaning) while the machine is running.
- Modularize equipment: Equipment portability and customization can reduce the number of interfaces or interactions, resulting in significantly faster changeover times. For example, designing equipment on skids can make each piece highly mobile.
- Streamline Remaining Elements
With your team, review the remaining elements on your list and discuss how you can simplify them. Remember that the goal is to reduce changeover time, so prioritize internal elements first. Use a cost/benefit analysis to decipher this. You can also create simultaneous operations to help streamline processes.
NASCAR pit crews are a great example of SMED because crew members can work on different car aspects at once (fueling, changing tires, inspection, etc).
Below is a visual to display how implementing SMED manufacturing can improve operations.
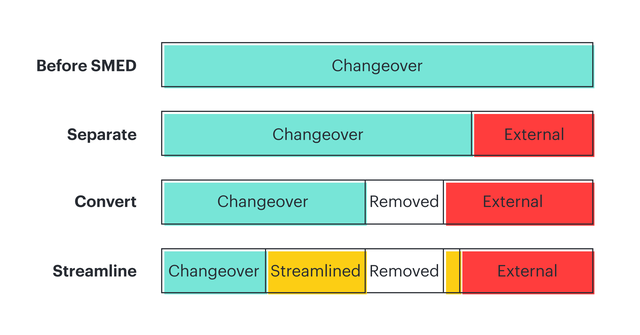
This 5-step process is information-heavy, so it is important to properly map out each step. Utilizing visual tools can be effective for monitoring and implementing the SMED process.
Tools that allow for team collaboration, data visualization, and scaling allow for a clear understanding of the processes and its goals.
With more teams moving to remote, adopting software that enables this is important for adopting the SMED process. Many tools are on the market however, it is vital to understand which ones are most effective for each project.
The takeaway
The implementation of SMED in your business can lower your manufacturing costs, reduce lot sizes, reduce finished goods inventory, improve responsiveness to customer demand, and improve equipment startups. This article aims to raise awareness of the processes in your company and to look at how these can be improved to decrease changeover time. Now that you have learned the steps for implementing SMED and how to properly track and monitor the success of this process, it’s time to put it into practice.
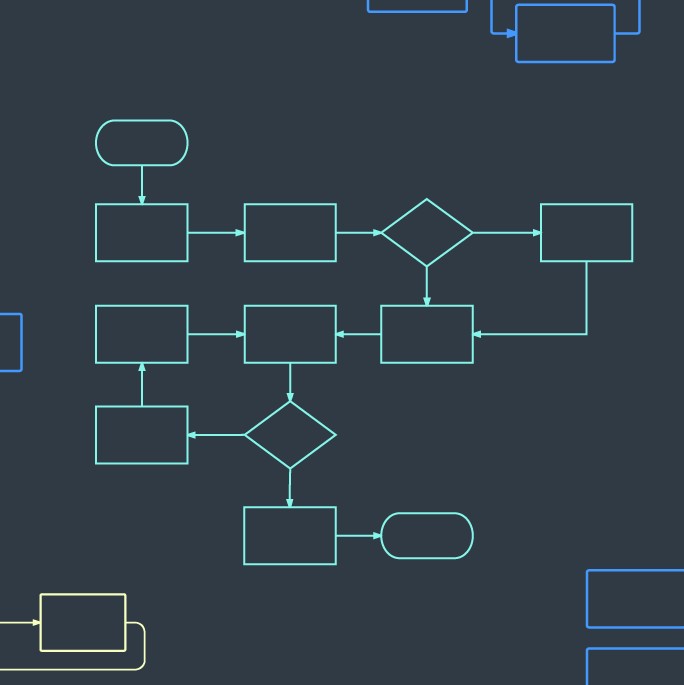
Learn more about how Lucidchart can help you see, improve, and scale your business processes.
Get startedAbout Lucidchart
Lucidchart, a cloud-based intelligent diagramming application, is a core component of Lucid Software's Visual Collaboration Suite. This intuitive, cloud-based solution empowers teams to collaborate in real-time to build flowcharts, mockups, UML diagrams, customer journey maps, and more. Lucidchart propels teams forward to build the future faster. Lucid is proud to serve top businesses around the world, including customers such as Google, GE, and NBC Universal, and 99% of the Fortune 500. Lucid partners with industry leaders, including Google, Atlassian, and Microsoft. Since its founding, Lucid has received numerous awards for its products, business, and workplace culture. For more information, visit lucidchart.com.