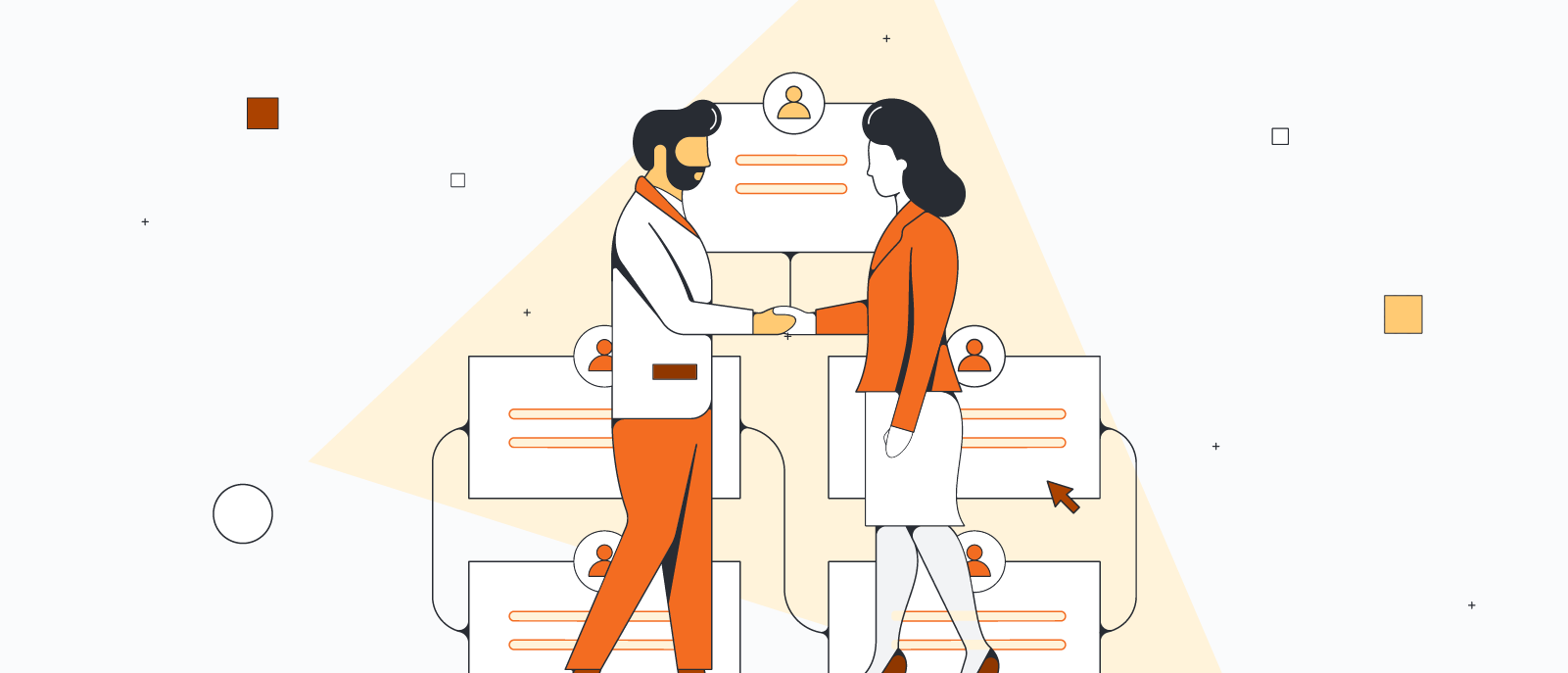
Six Sigma process mapping: Why it matters and how to get started
Reading time: about 6 min
Topics:
In a past blog post, we broke down the different types of process improvement methodologies and the diagrams you might use to follow any of these methods. Now we want to take a deep dive into one of the most-used techniques we discussed: Six Sigma process mapping.
Learn what a process map is, how it fits into the Six Sigma methodology, and how you can easily build one using a process mapping tool.
How process mapping works for Six Sigma
As a reminder, Six Sigma originated in 1986 as a data-driven approach for increasing the quality of products and services by eliminating defects from any process. Companies using Six Sigma aim for 99.99966% of their products to be free of defects (we know, it’s pretty specific).
To achieve this goal, companies need to follow the DMAIC process, a Six Sigma process improvement methodology. Here are the five steps:
- Define the problem, area for improvement, or customer requirements.
- Measure performance of the current process.
- Analyze the process to determine the root cause of defects or inefficiencies.
- Improve performance by eliminating the root cause.
- Control the improved process to ensure high performance.
Process mapping enters at the very first stage. Anyone involved with optimizing processes or eliminating defects needs to first define the process and understand it completely. A Six Sigma process map outlines each step of the process graphically to make it faster and easier to understand.
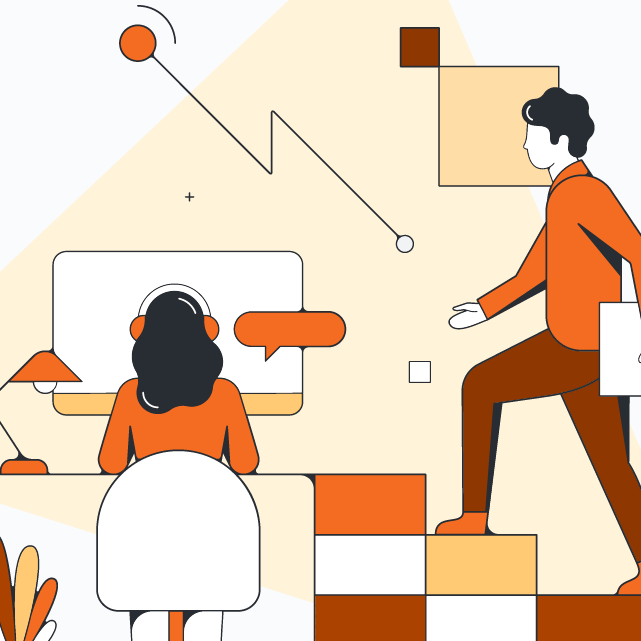
Learn more about process maps and how to improve your business processes.
Read nowBenefits of process mapping
You already have a lot of work ahead of you as you cut waste from your company’s operations—why dedicate resources to create a flowchart showing your whole process? Because Six Sigma process mapping can actually save you time through these benefits:
-
See the entire process in one view. Visualizations make abstract concepts, like processes, tangible so people can grasp ideas faster. Instead of verbally walking through the process or reading explanations of individual steps, you can see the whole process at one time on a process map.
-
Detect waste faster. By visualizing the process, you can pinpoint areas that do not add value or that lower efficiency. And as we’ll discuss later, you can also build a map of your future state and compare it with your current state.
-
Deliver on promised expectations. The Six Sigma process comes down to quality. You want to eliminate defects so your customers receive exactly the products and services they expect to receive when they expect to receive them. Six Sigma process mapping forces you to see your process as it really happens so you can see where you may fall short of those expectations.
-
Store updated processes for future reference and training. Once you’ve found and corrected defects, train new hires on the new process or send it around your office so everyone remembers the correct protocol.
Six Sigma process maps
Depending on the process you’re examining or your project goals, you may need to drill down and precisely document every single step, or you may just need a brief overview to show stakeholders. Whatever your situation, reap the benefits of Six Sigma process mapping with the help of these process maps.
SIPOC
SIPOC, which stands for suppliers, inputs, process, outputs, and customers, gives you a high-level overview of your process and its contributing components. As it includes other information on top of your process, use this diagram at the beginning of a process improvement initiative or before delving into more detailed process mapping.
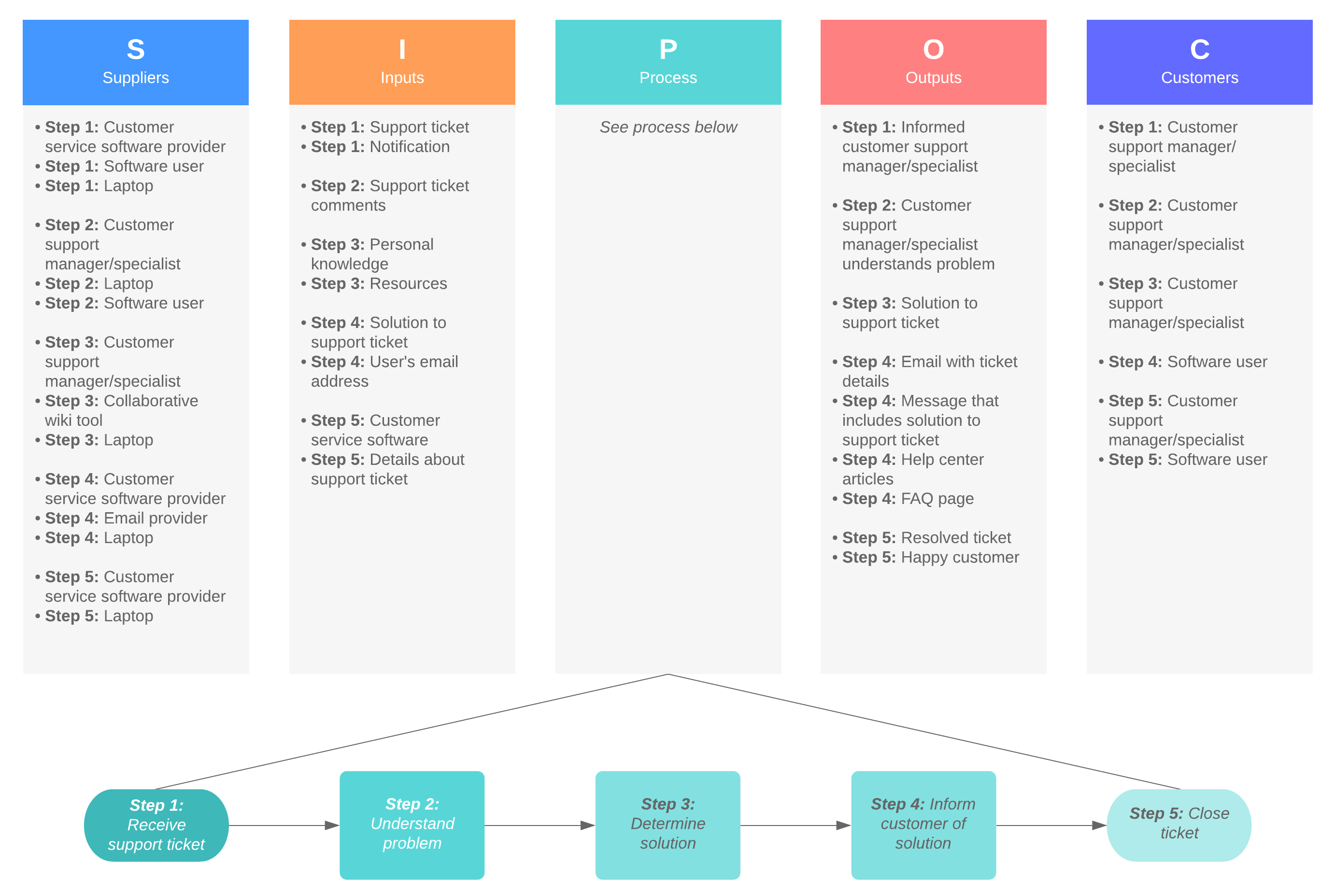
High-level process map
The high-level process map illustrates the basic steps in your process so you can quickly and easily understand it without having to get down in the weeds. This map is valuable when working with executives or managers, since they often need to see what’s going on but don’t always need all the specifics involved in a process.
Detailed process map
As the name suggests, a detailed process map helps you see all the details. Because it includes so much information, this process map is especially important for finding the root cause of errors or waste in a process. You will likely need to involve the employees who perform the process since they will have the most knowledge about it.
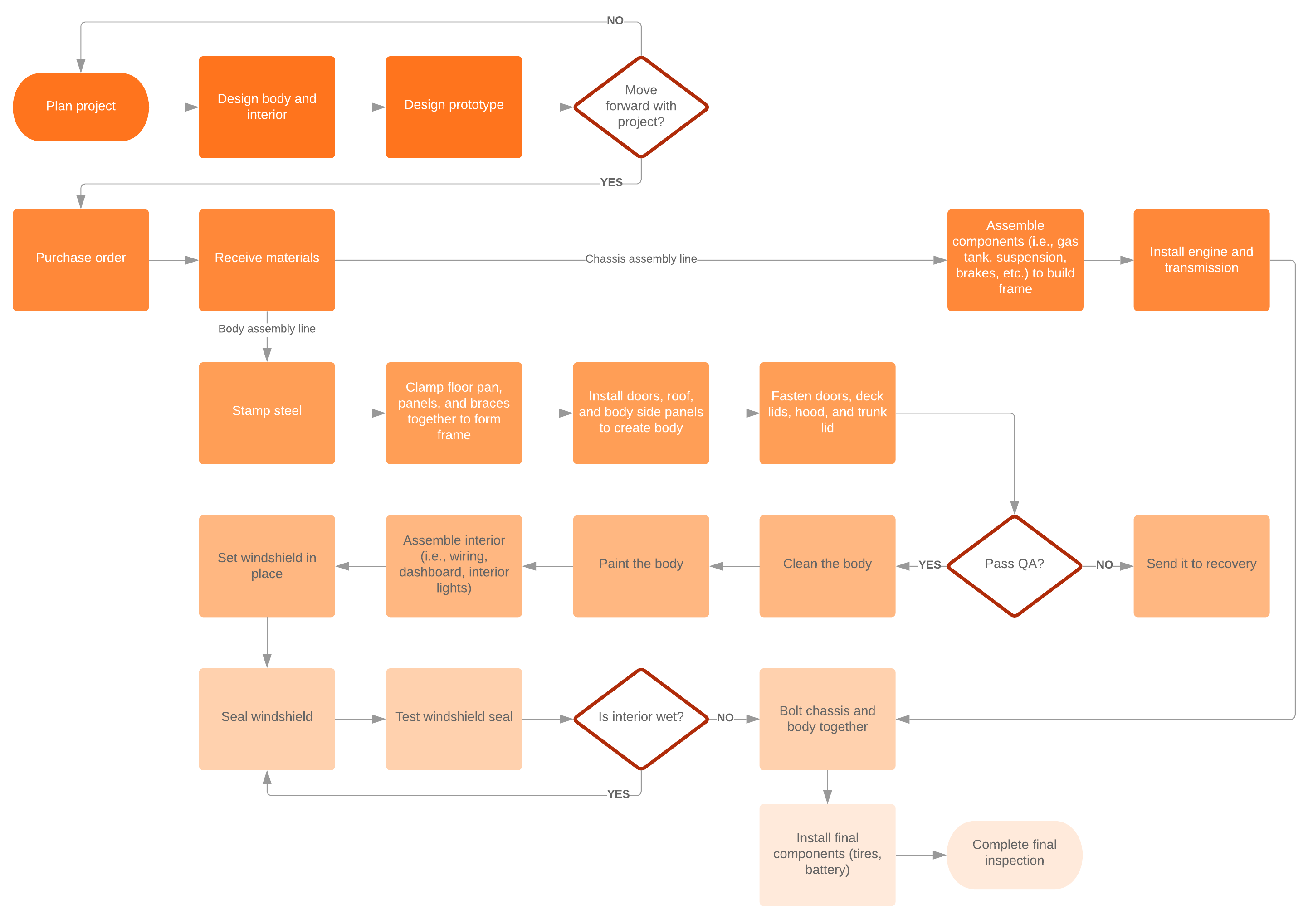
Ready to create a high-level or a detailed process map?
Get started with our templateSwimlane diagram or deployment flowchart
A swimlane diagram, also known as a deployment flowchart, divides the process by the person or team who is in charge of that stage. As well as showcasing cross-functionality, this kind of process map clarifies where handoffs occur, which may not be as clear in other process maps.
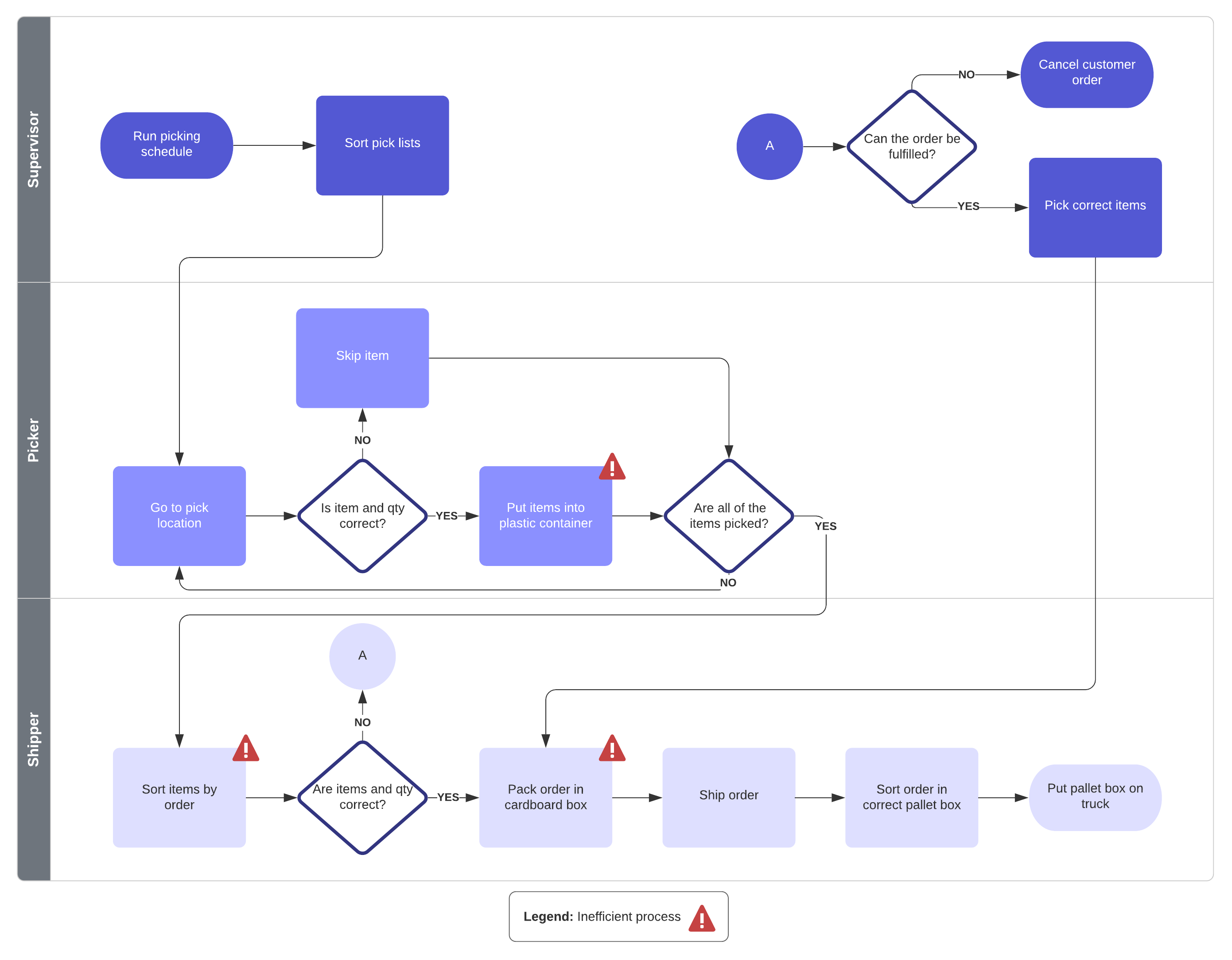
Value stream map
Created as part of Lean implementation and process improvement, a value stream map is a process map that illustrates and analyzes the steps involved in producing a product or delivering a service. It’s a detailed diagram that displays a process’s current state, focusing on valuable or non-value added activities in the process. Try Lucidchart's value stream map template to create a value stream map in minutes.
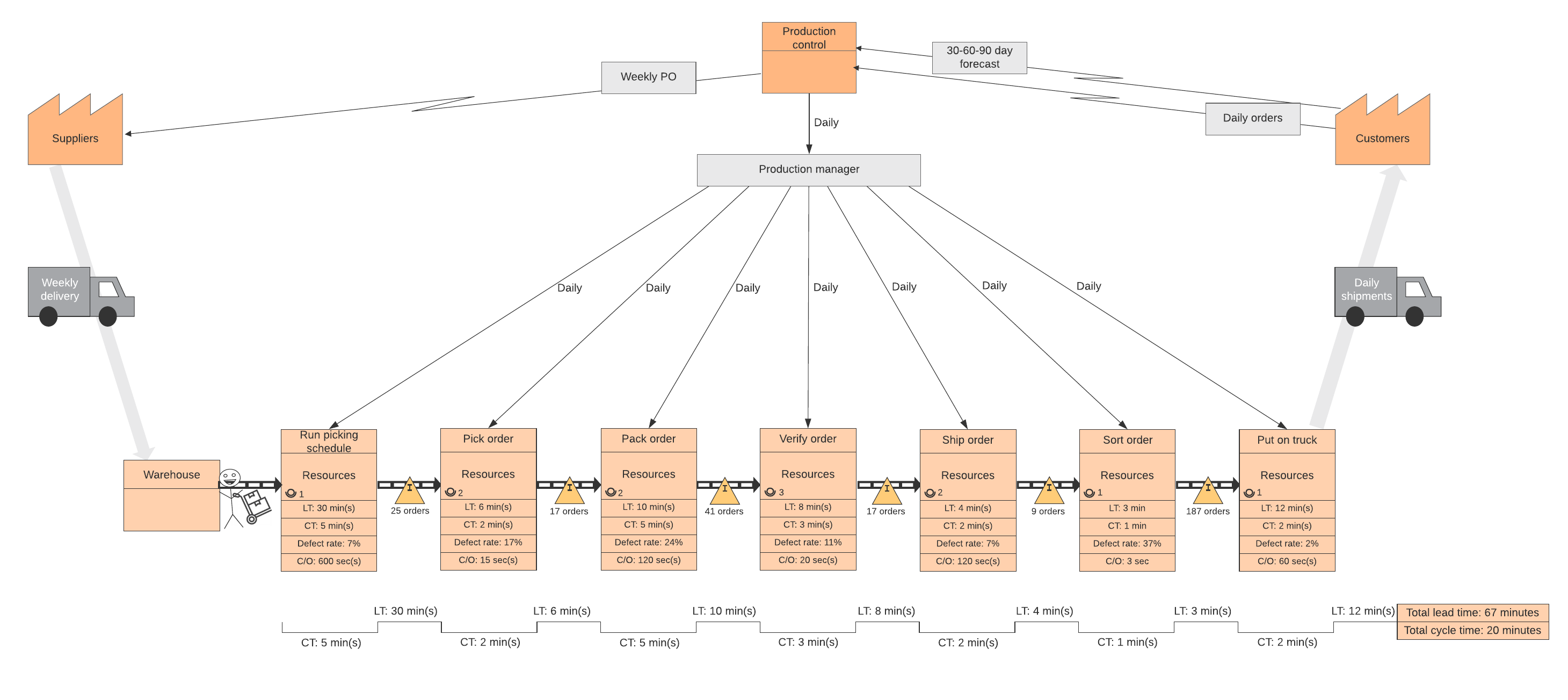
How to create a process map in Six Sigma
Now that you have some options in front of you, it’s time for you to build one of these process maps. Let’s walk through the steps of Six Sigma process mapping.
1. Determine context and scope
What do you want to accomplish with this process map? Which process or part of a process do you need to review? Once you understand how you want the process map to help you, you can choose a type of process map and decide how much detail it should cover.
2. Identify and sequence the steps of your as-is process
With the purpose and scope of your Six Sigma process map in mind, set the start and end points of your process. Add other shapes to represent process steps, inputs, outputs, transportation of materials, etc. Use process mapping symbols to visually differentiate these different steps.
3. Ask others to review the map for accuracy
Send your Six Sigma process map to people in different teams to make sure that all your information is accurate. You could even walk through the process yourself, with your process map in tow, to see whether you covered every step.
4. Analyze the process map and single out pain points
So you have an accurate visualization of your process. Great! Now you can refer to this document as you ask questions about the process. Are there steps you can remove or combine? Do you see any redundancies? If you have delays throughout the process, why are they happening?
Keep asking yourself why the process functions the way it does. Make notes on or edit your process map to track the changes you want to see.
Optional: Create a new process map with your ideal state
Six Sigma process mapping can help you beyond visualizing your current state—you can also use this practice to map out your process as you would like it to be. With this ideal process in hand, you can compare the two diagrams and determine how to move your current state closer to the future state.
Whether you’re looking to optimize how you generate leads or understand your user flows, visually mapping your processes helps you attain your Six Sigma goals. Try out our tips and process map templates to reduce defects and ensure that you deliver quality in every process.
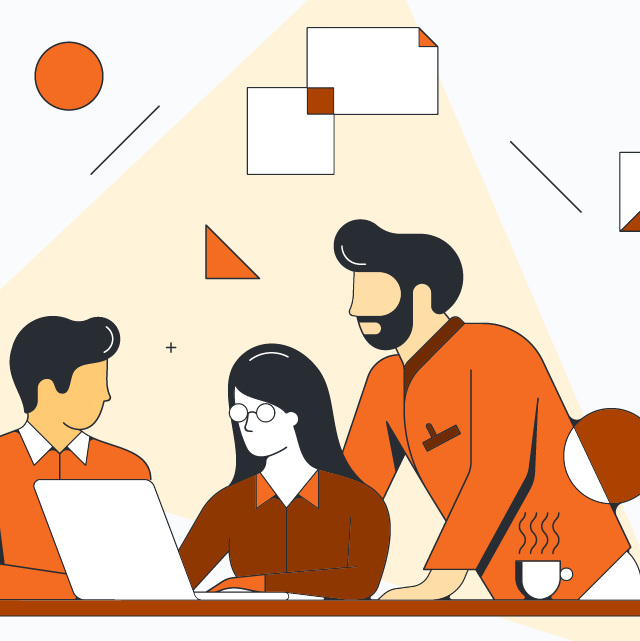
Map out your business processes and be more efficient with Lucidchart.
Learn moreAbout Lucidchart
Lucidchart, a cloud-based intelligent diagramming application, is a core component of Lucid Software's Visual Collaboration Suite. This intuitive, cloud-based solution empowers teams to collaborate in real-time to build flowcharts, mockups, UML diagrams, customer journey maps, and more. Lucidchart propels teams forward to build the future faster. Lucid is proud to serve top businesses around the world, including customers such as Google, GE, and NBC Universal, and 99% of the Fortune 500. Lucid partners with industry leaders, including Google, Atlassian, and Microsoft. Since its founding, Lucid has received numerous awards for its products, business, and workplace culture. For more information, visit lucidchart.com.
Related articles
Limitations of Six Sigma Steps and What to Do About Them
Learn how to follow the Six Sigma steps, where the limitations of the methodology lie, and what methodologies you may want to use instead.
Six Sigma tools you need to improve your processes
Whether you need to perform root cause analysis or control quality, we've got the ultimate list of Six Sigma tools that can be easily applied to any project or organization. Templates included!