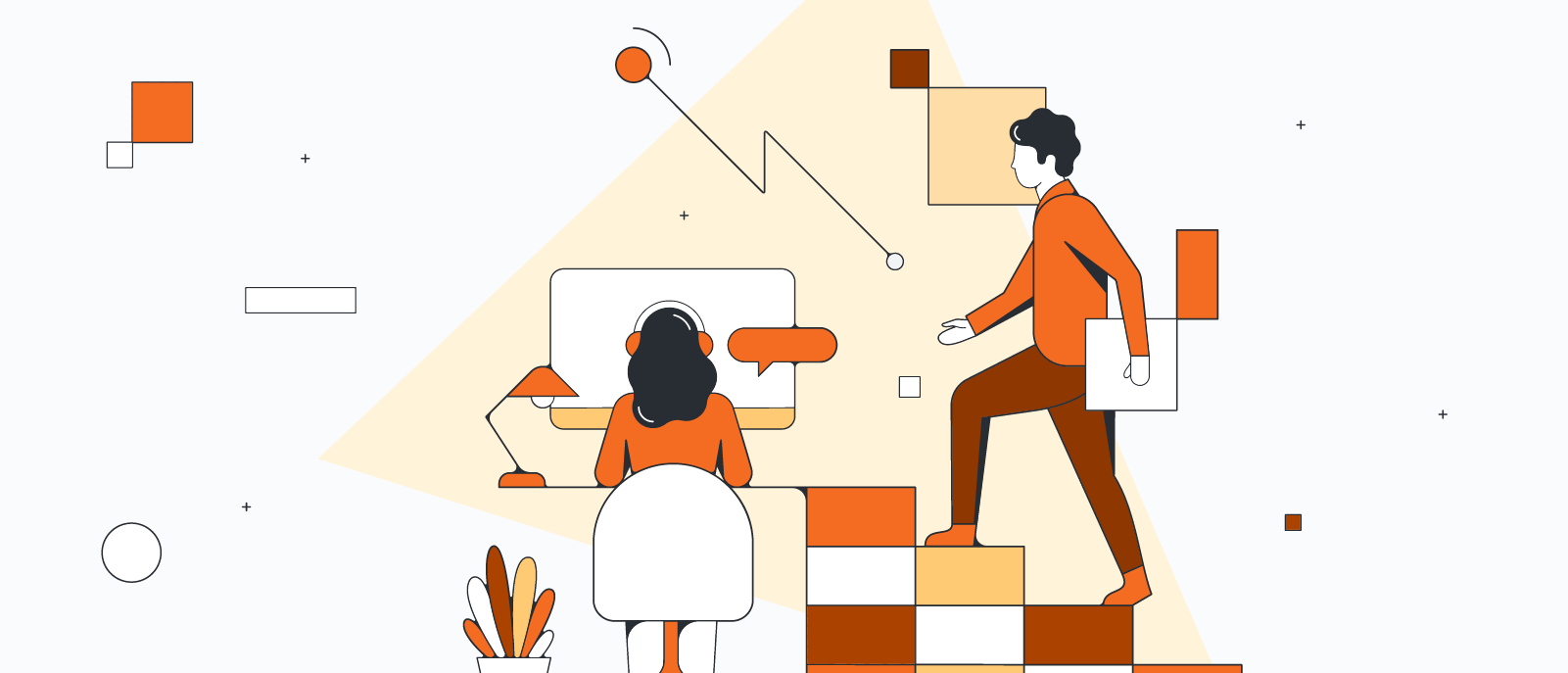
How to apply the Plan-Do-Check-Act (PDCA) model to improve your business
Reading time: about 7 min
Most businesses want to improve. But when it comes to actually making needed changes, many fall short. Bureaucracy, silos, and even culture can block progress and stall innovation.
The Plan-Do-Check-Act model helps break companies out of stagnancy and transition to a system of continuous improvement. Learn how the PDCA cycle works and what benefits you can gain from using it at your company.
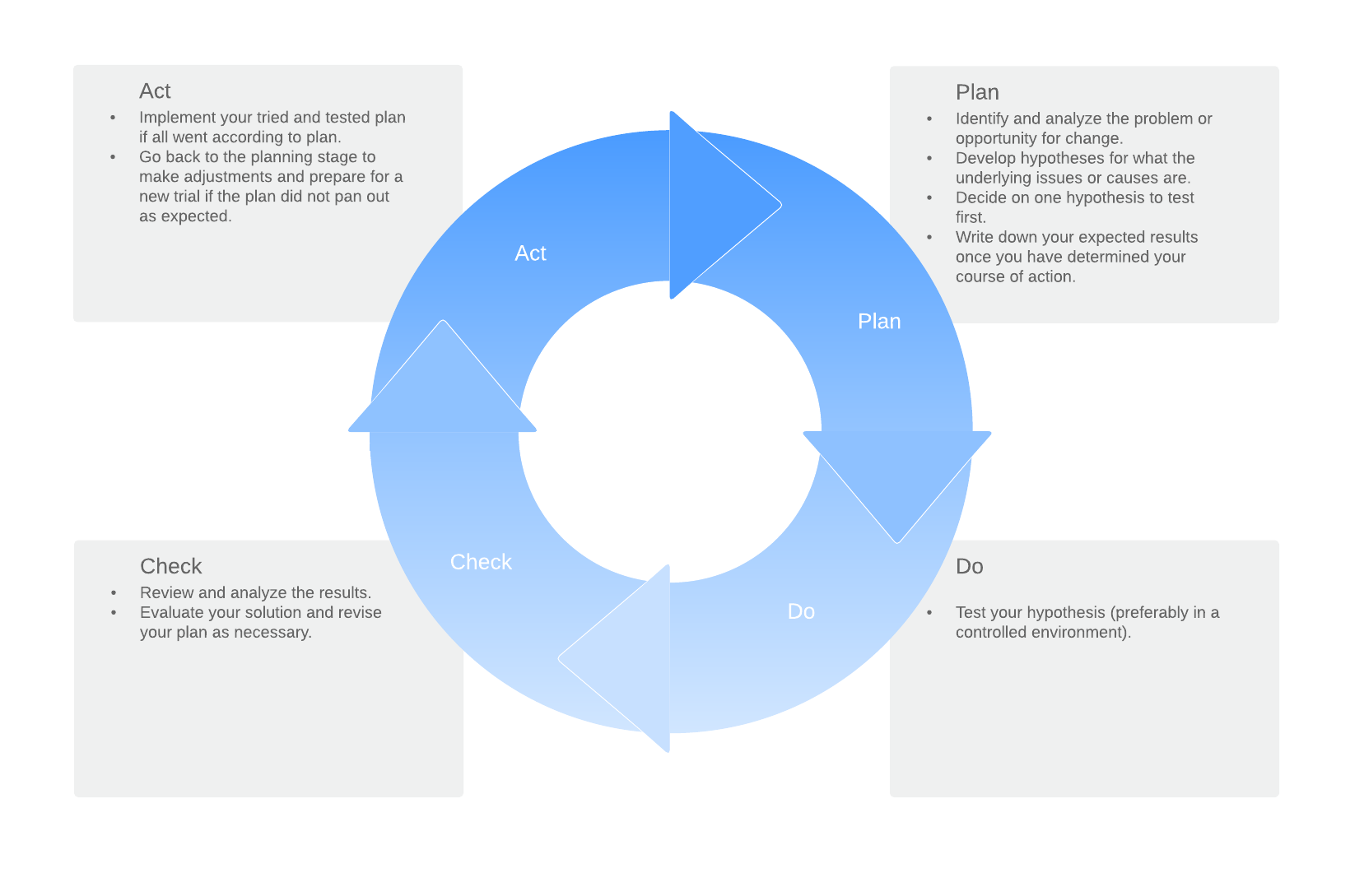
What is PDCA?
The Plan-Do-Check-Act (PDCA) model, also known as the Deming wheel or the Deming cycle, is an iterative method for continual improvement of processes, products, or services and is a key element of lean management.
The PDCA model was developed in the 1950s by William Deming as a learning or improvement process based on the scientific method of problem-solving. Deming himself called it by another term—the Shewhart cycle—because he created the model based on an idea from his mentor, Walter Shewhart.
As all of these names suggest, the PDCA cycle is a loop rather than an end-to-end process. The goal is to improve on each improvement in an ongoing process of learning and growth.
When should you use the PDCA process?
The Plan-Do-Check-Act model is a helpful tool that can be used for a number of applications:
- Exploring and testing multiple solutions in a small, controlled trial
- Avoiding waste by catching and adapting ineffective solutions before rolling them out on a large scale
- Implementing change and continuous improvement
- Implementing Total Quality Management or Six Sigma initiatives
- Developing or improving a process
What is great about the PDCA cycle is that it can be applied across industries and organizational types.
Pros and cons of PDCA
The PDCA cycle has a number of advantages and disadvantages. Consider both before you decide to apply Plan-Do-Check-Act to different projects.
Pros
Versatile: You can use PDCA in a variety of business environments and for a number of applications. Potential use cases include project management, change management, product development, and resource management.
Simple and powerful: The PDCA model is simple and easy to understand, yet it is a powerful driver for meaningful change and improvement while minimizing waste and increasing efficiency.
Cons
Hard to do: Though the model is simple, the work isn’t easy. Because PDCA breaks process improvements into smaller steps, it can be slow and probably isn’t a great solution for urgent projects.
Requires commitment: PDCA is not a one-time event. It is an ongoing, continuous process and therefore requires commitment and buy-in from the top down. Without committed leadership, the PDCA cycle can’t work effectively for the long term.
The PDCA model
Sold? Learn the four stages in the PDCA cycle (which you can probably guess from the name) to start using it.
1. Plan
The planning stage is for mapping out what you are going to do to try to solve a problem or otherwise change a process. During this step, you will identify and analyze the problem or opportunity for change, develop hypotheses for what the underlying issues or causes are, and decide on one hypothesis to test first.
As you plan, consider the following questions:
- What is the core problem we need to solve?
- Is this the right problem to work on?
- What information do we need to fully understand the problem and its root cause?
- Is it feasible to solve it?
- What resources do we need?
- What resources do we have?
- What are some viable solutions?
- What are the measures of success?
- How will the results from a small trial translate to a full-scale implementation?
During this stage, an affinity diagram can help you and your colleagues organize a large number of ideas into groups. Once you have determined your course of action, write down your expected results. You will check your results against your hypothesis and expectations in the “Check” stage.
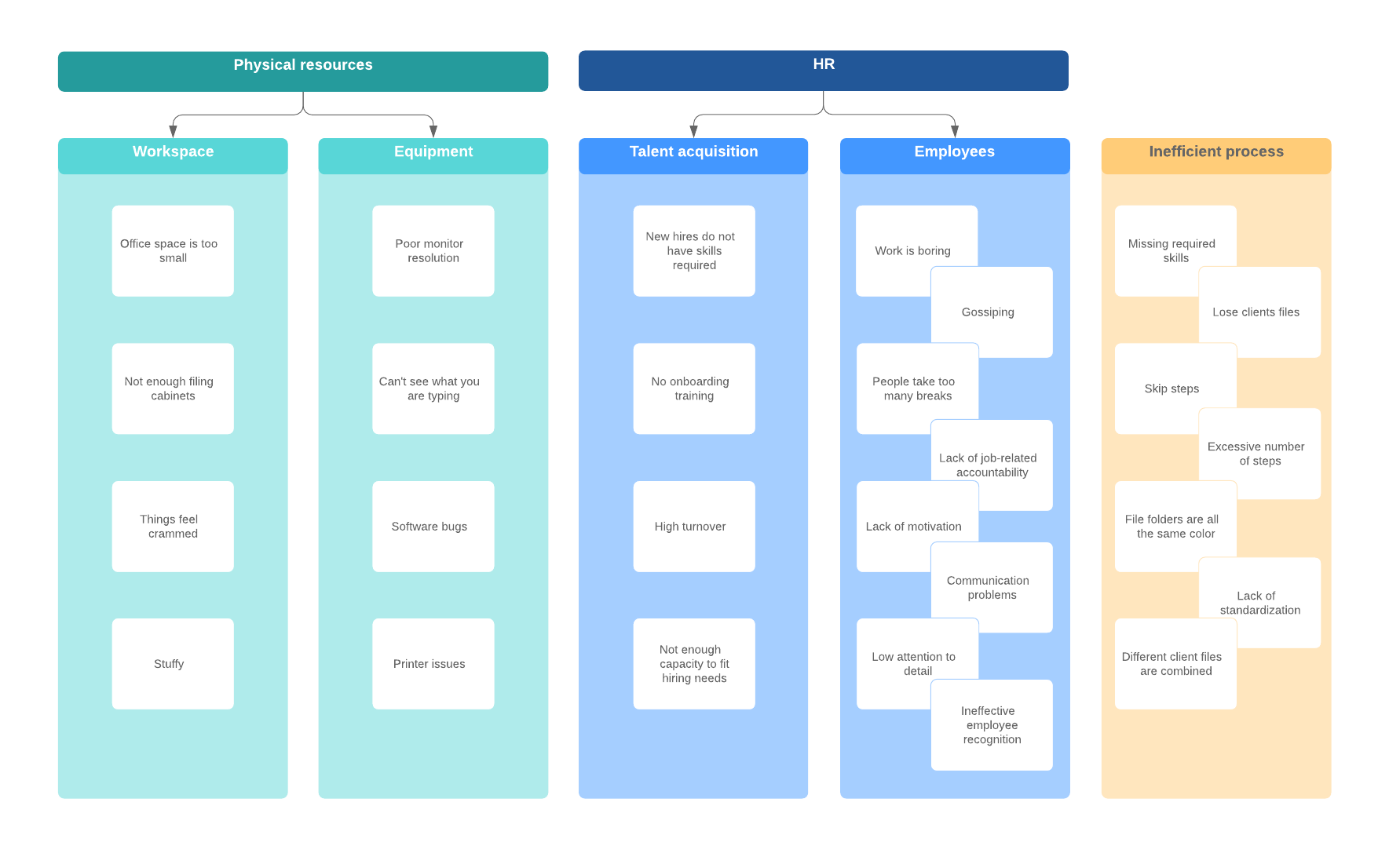
2. Do
The next step is to test your hypothesis (i.e., your proposed solution). The PDCA cycle focuses on smaller, incremental changes that help improve processes with minimal disruption.
Test your hypothesis with a small-scale project, preferably in a controlled environment, so you can evaluate the results without interrupting the rest of your operation. You might want to test the solution on one team or within a certain demographic.
3. Check
Once you have completed your trial, it’s time to review and analyze the results. This stage is important because it allows you to evaluate your solution and revise your plans as necessary. Did the plan actually work? If so, were there any hiccups in the process? What steps could be improved or need to be eliminated from future iterations?
Your evaluation at this stage will guide your decisions in the next step, so it is important to consider your results carefully.
4. Act
Finally, it is time to act. If all went according to plan, you can now implement your tried-and-tested plan. This new process now becomes your baseline for future PDCA iterations.
Consider the following questions before you act:
- What resources do you need to implement the solution at full scale?
- What training is needed for successful implementation and adoption?
- How can you measure and track the performance of the solution?
- What opportunities are there for improvement?
- What have we learned that can be applied to other projects?
If the plan did not pan out as expected, you can cycle back to the planning stage to make adjustments and prepare for a new trial.
Plan-Do-Check-Act example
So what does the PDCA model look like in action?
In 2019, the Department of Obstetrics and Gynecology at the Ningbo Women and Children’s Hospital in China applied the Plan-Do-Check-Act model to shorten the emergency decision to delivery interval (DDI) time. This is the time it takes between the decision to conduct a caesarean section and the delivery of a newborn. Shortening this time period in emergency situations is critical to saving lives and improving patient outcomes.
Here’s how they did it:
Plan: In 2019, the hospital had an average DDI time of 14.40 minutes. Their process analysis identified three main causes impacting DDI time:
- A defective process
- Lack of first-aid experience
- Poor cooperation among departments
Do: The team developed improvement measures for each cause including:
- Simplifying the surgical process to speed up the pre-op routine
- Establishing a special DDI team to respond to emergency situations
- Standardizing DDI team working processes
- Creating an emergency treatment team, featuring senior doctors with clinical first-aid experience
- Implementing a variety of regular training, such as obstetrical safety meetings, emergency C-section process classes, and practical and theoretical trainings
- Conducting multi-department emergency treatment drills
Check: The hospital monitored and analyzed progress monthly, creating regular evaluation summaries and refining the cause analysis and improvement measures over time.
Act: After refining their processes, the hospital’s improvements optimized C-section delivery processes, increased collaboration across departments, and shortened the average emergency DDI to 12.18 minutes in 2020.
Supporting Kaizen with the PDCA cycle
The Plan-Do-Check-Act model is a particularly useful tool for companies who follow the Kaizen method. Kaizen is an organizational mindset and culture focused on small, frequent changes that lead to significant improvements over time.
The PDCA cycle supports the Kaizen philosophy by providing the framework for developing and implementing continuous improvements.
Using Lucidchart to continuously improve
Lucidchart is a visual workspace that helps teams and companies map out their processes and visualize their data in new ways. Use Lucidchart to visualize your PDCA cycle and help you through each step of the process. As you plan your project, you can create a fishbone (cause-and-effect) diagram to visualize problems and potential causes.
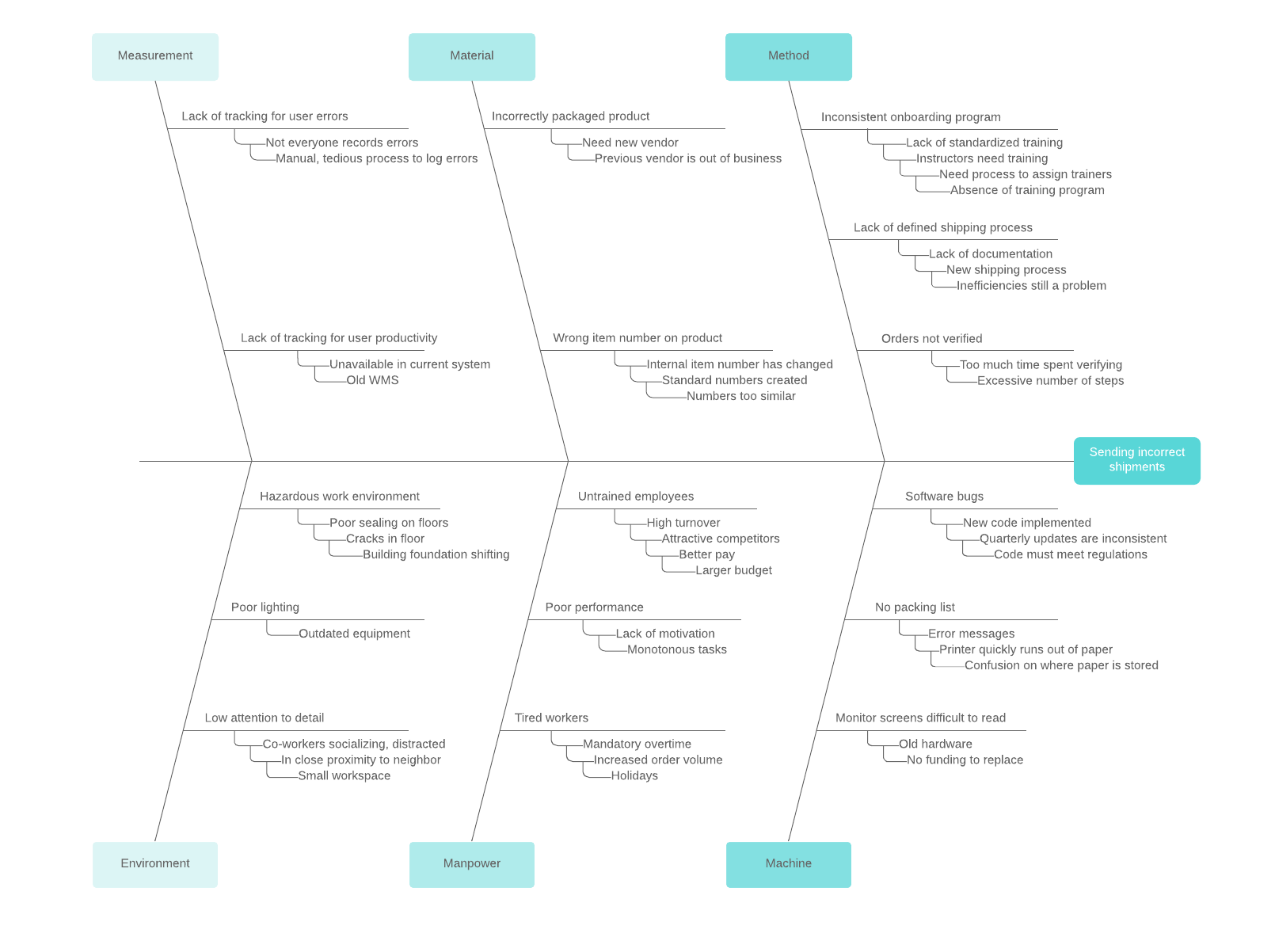
During the “Do” stage, map out the new processes you plan to try. Use data linking to connect real-time data to your diagrams and keep track of your results. Once you have a solution you’re ready to implement, use Lucidchart to create diagrams visualizing the new processes. Lucidchart makes it easy to share documents with your team so they can quickly learn and understand the changes.
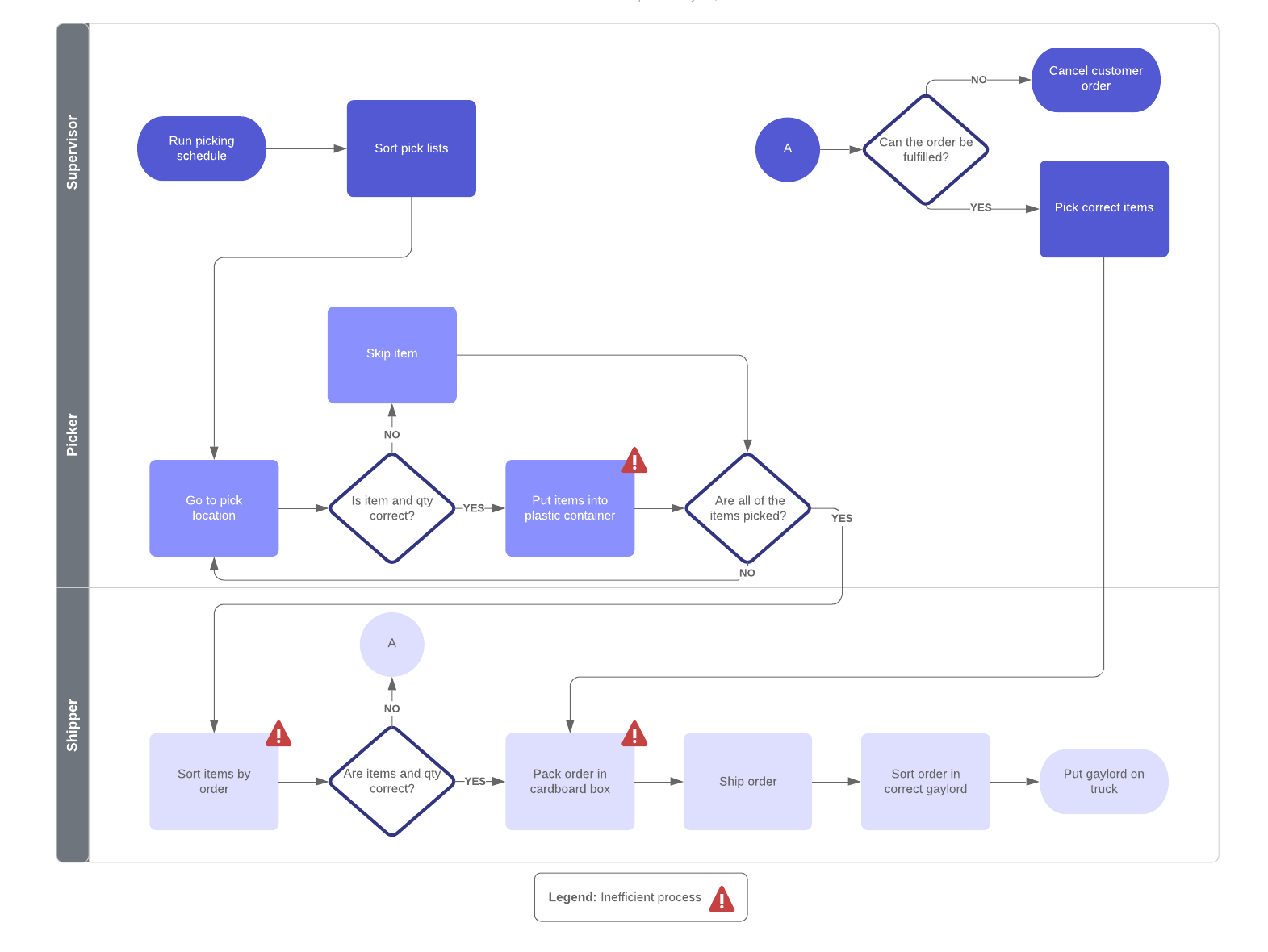
If you’re continuously improving, it can be easy to lose track of your changes over time. Keep everyone on the same page by documenting your continual progress in Lucidchart.
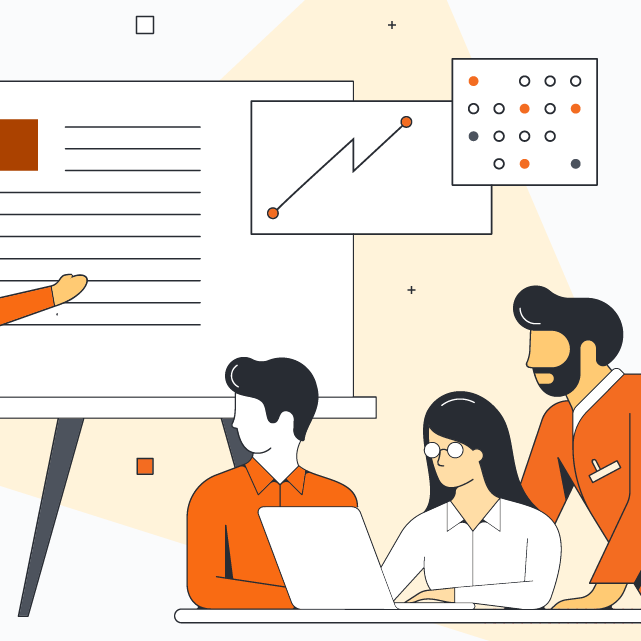
Learn more about how to elevate your business.
Go nowAbout Lucidchart
Lucidchart, a cloud-based intelligent diagramming application, is a core component of Lucid Software's Visual Collaboration Suite. This intuitive, cloud-based solution empowers teams to collaborate in real-time to build flowcharts, mockups, UML diagrams, customer journey maps, and more. Lucidchart propels teams forward to build the future faster. Lucid is proud to serve top businesses around the world, including customers such as Google, GE, and NBC Universal, and 99% of the Fortune 500. Lucid partners with industry leaders, including Google, Atlassian, and Microsoft. Since its founding, Lucid has received numerous awards for its products, business, and workplace culture. For more information, visit lucidchart.com.
Related articles
How to Use Kaizen Methodology to Improve Business Processes
The Kaizen methodology is an easy way to engage employees and develop a culture of continuous improvement. It strives to eliminate silos, egos, and waste and instead aims for efficient and standardized processes. See why you should use Kaizen and how you can get started.
7 essential steps to create a process improvement plan [+templates]
No matter how good the idea, changes won't last without a solid process improvement plan in place. Learn the essential steps involved with every process improvement plan.