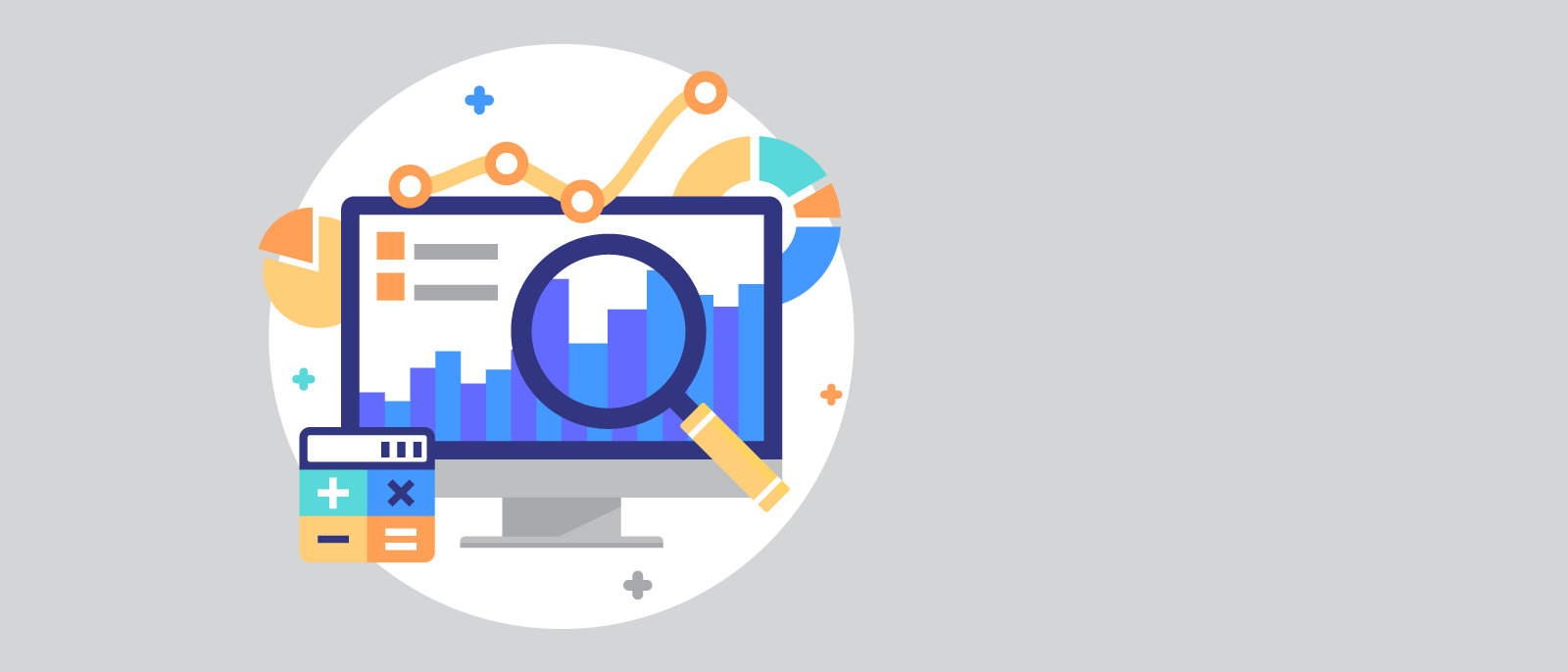
Lean vs. Six Sigma: Determining the Right Method for Your Business
Lucidchart Content
Reading time: about 9 min
Topics:
When it comes to modern business, the name of the game is efficiency. Smart companies are focused on minimizing waste and continuously improving processes to ensure the business runs as smoothly and cost-effectively as possible.
Lean manufacturing and Six Sigma are two popular process improvement methodologies that can help in this effort. Let’s define each, break down their history, and show you how to implement these methodologies to help you determine the right approach for your business.
Difference between Lean and Six Sigma
The goal of Six Sigma and Lean is to eliminate defects and waste, thereby streamlining and improving all business processes to improve quality and efficiency. However, each of these methodologies take a different approach—so understanding their definitions is critical to selecting the method appropriate for your business goals.
What is Lean manufacturing?
When you think of an assembly line, you might think of the model of efficiency implemented by Henry Ford and his auto factory at the turn of the 20th century. Considered “the father of Lean manufacturing,” Ford drove himself and his company to create operational efficiencies and, as a result, better products.
What makes this process so successful? The main emphasis of Lean is cutting out unnecessary and wasteful steps that don’t add value to the creation of the final product. The result is a highly efficient, streamlined, and profitable manufacturing process.
The Lean philosophy has five fundamental principles:
- Value
- Value stream
- Flow
- Pull
- Perfection
These five steps work to create a culture of continuous improvement at your facility and enable teams to respond more quickly to shifting customer requirements, without massive reshufflings or slowdowns.
1. Identify value
Before you create any product, you should clearly define its value to the market. What customer need will you fulfill? Determine the value and demand of your product to eliminate any manufacturing costs that won’t directly tie back to revenue.
2. Map out value stream
In a value stream map, lay out all of the steps and materials needed to deliver a product to your customer. This Lean step will help you analyze delays and inefficiencies to help you eliminate any wasteful steps in the process.
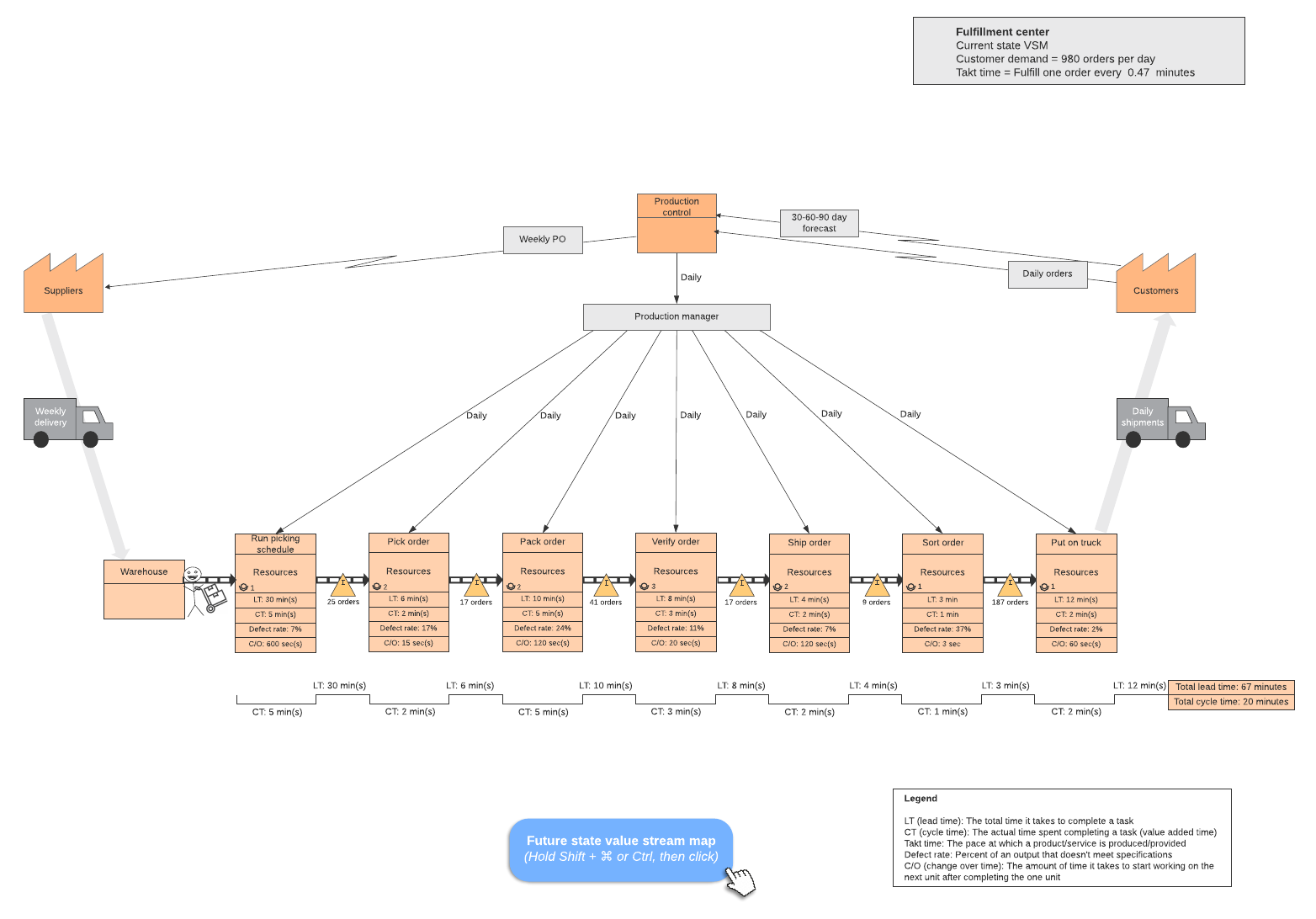
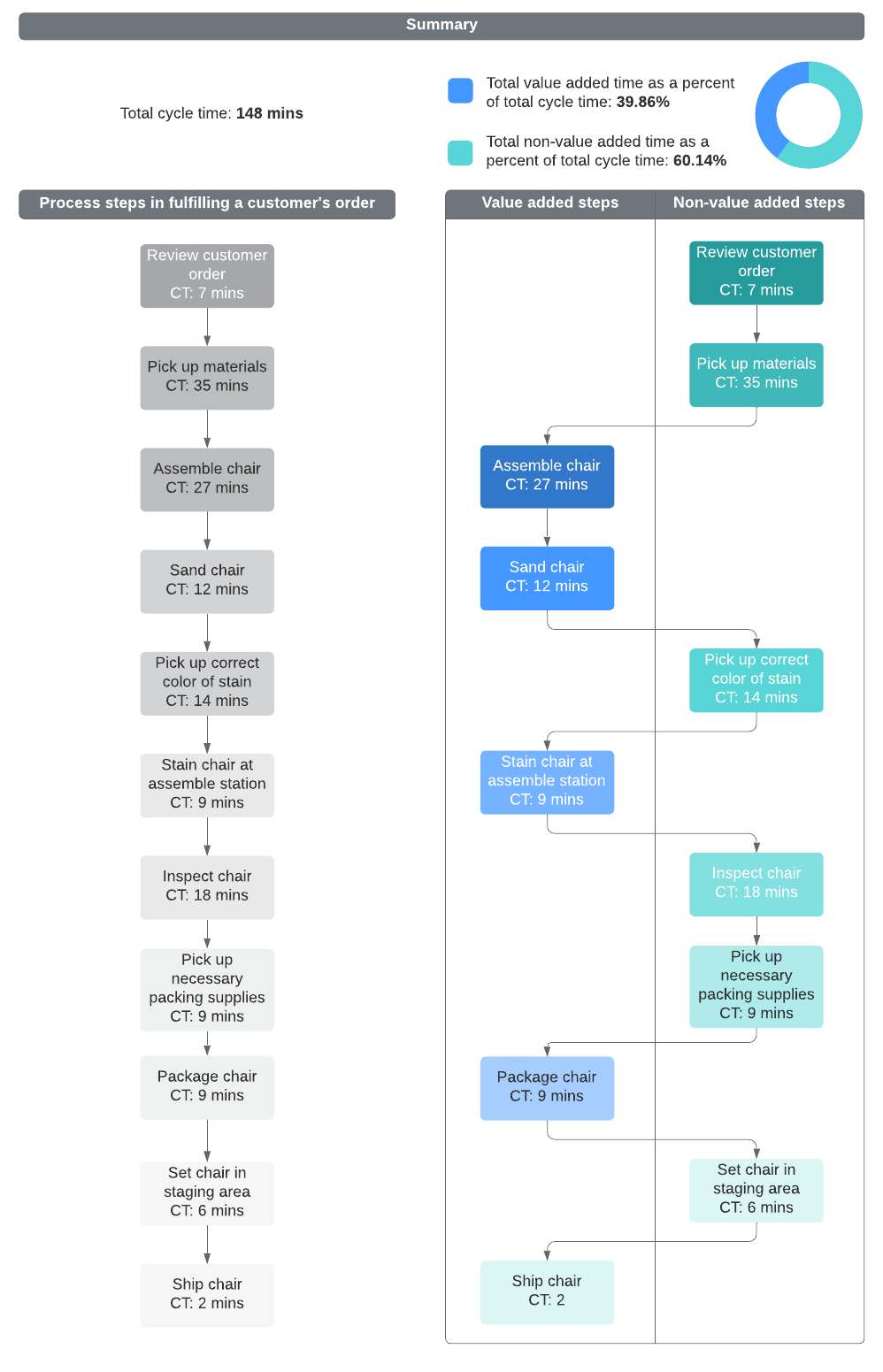
3. Create process flow
Once your value stream is defined, ensure each step follows a repeatable process. This Lean manufacturing principle will enable clean, synchronized production, and smooth delivery to your customers.
4. Establish pull
This principle is about ensuring you have demand or orders from your customers before you begin production. Only then do you “pull” parts needed to deliver the product to your customers. “Pulling” creates an on-demand process that helps manage inventory and minimize waste.
5. Continuously improve and perfect
Test, learn, and optimize. This Lean principle involves consistent monitoring and evaluation of your process to ensure you’re set up for maximum quality output and minimum waste.
What is Six Sigma?
In the 1980s, Motorola engineer Bill Smith found that eliminating variation can help you improve the customer experience and minimize costs. Similarly to Lean, the Six Sigma methodology also looks to reduce waste.
However, Six Sigma defines waste as anything that doesn’t meet the customer’s expectations and focuses more on eliminating any inconsistencies in the customer experience. While first designed for use in manufacturing, Six Sigma can also apply all aspects of the business.
What makes this process so successful? The idea of sigmas comes from standard deviation, and the goal of a Six Sigma methodology is to reduce variance as much as possible and reduce defects by parts per million. When you’re operating at Six Sigma, you’re only experiencing 3.4 defects per million units.
The result is a process that helps all types of businesses run more smoothly and efficiently. The Six Sigma methodology involves seven fundamental principles, some of which overlap with the Lean manufacturing model:
1. Focus on the customer
Like the Lean model, value should be a primary focus. Focusing on the customer first will help you optimize the production process and deliver a product the customer wants to buy.
2. Understand how work happens
Without a clear understanding of current processes, it’s tough to make any improvements. Process maps and workflow charts can help you define your existing processes and identify any inefficiencies.
3. Make your processes flow smoothly
This is the core principle of Six Sigma. Once you’ve identified bottlenecks, you can implement a process like the 5 Whys analysis to understand why the inefficiencies exist and come up with a plan to address them.
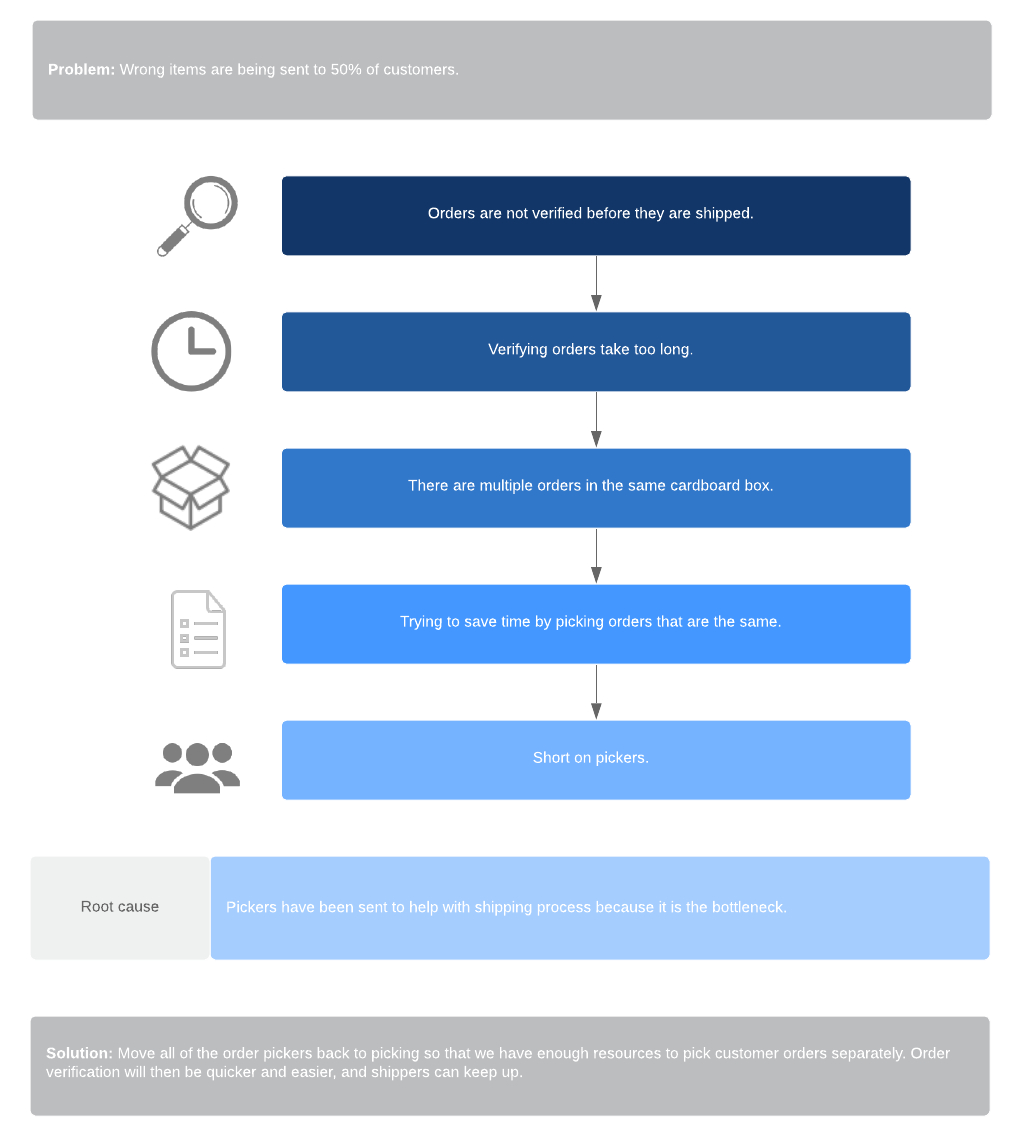
4. Reduce waste and concentrate on value
Similar to Lean, the focus should be on delivering value—and that means cutting out waste or duplicative work.
5. Stop defects through removing variation
A process that is predictable and repeatable will help minimize errors and keep operations running smoothly. Process maps can also be used by manufacturers and marketers alike to standardize processes.
6. Get buy-in through collaboration
Including people across the company in the improvement process will help you spot any blindspots or hidden variations and work together to create the most efficient process.
7. Make your efforts systematic and scientific
At its core, Six Sigma is a data-driven methodology. Each of the principles above gives you the data and insights needed to adequately define a problem, calculate potential ROI, and measure your progress toward it.
How to implement Six Sigma vs. Lean
Still unsure which methodology is right for your business? Understanding how Lean and Six Sigma are implemented may help you more clearly see which will meet your business’s needs and goals.
Many facilities implement Lean manufacturing using the 5S model (note that some industries have added a sixth “S” for safety) to eliminate waste from manufacturing processes and improve bottom-line results. Let’s break this process down:
- Sort: Remove items that are no longer needed and streamline resources.
- Straighten: Organize resources to optimize efficiency and flow
- Shine: Clean and organize the space to more easily identify inefficiencies and see processes more clearly
- Standardize: Implement standardized processes such as color-coding or labels to help processes stay consistent, efficient, and repeatable
- Sustain: Set benchmarks and plans and encourage behaviors to keep workplaces and facilities organized and productive over time.
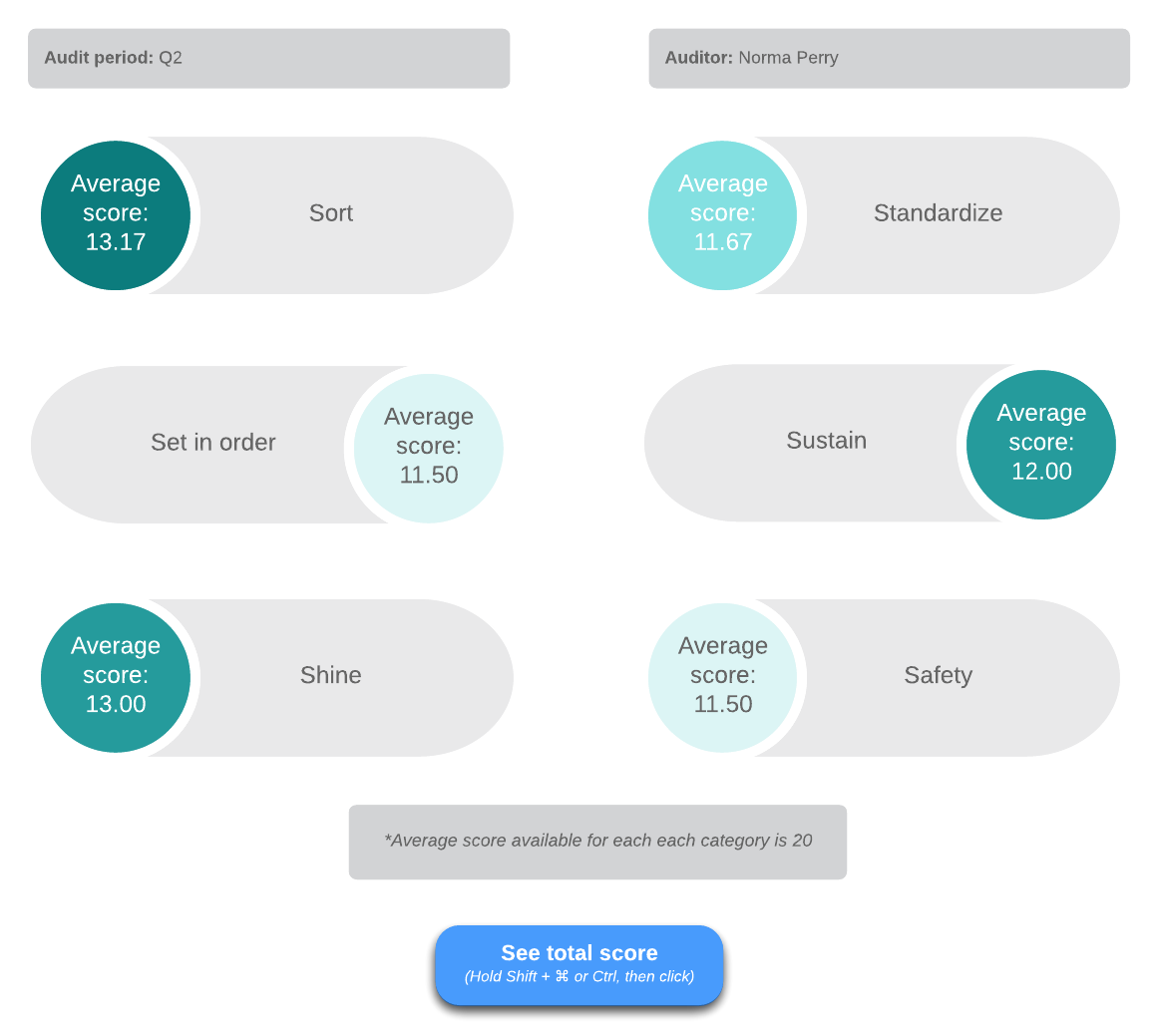
Six Sigma implements process improvement using DMAIC, which stands for define, measure, analysis, improvement, and control. This process has many similars with the 5S model but takes a more data-driven approach at problem-solving and implementation. Here is a more in-depth look at each step of the process:
- Define: Define the problem by mapping out current processes and noticing any inefficiencies.
- Measure: Take a hard look at the data by examining the process currently in place and identify any points of inefficiencies.
- Analysis: Once you’ve measured your data, you can use data-driven insights to help identify what’s not working so you can optimize your process.
- Improvement: Start to build your optimization plan. What improvements can you make to maximize inefficiency and improve results?
- Control: Optimization never ends. Once you’ve got a successful, efficient plan in place, it’s essential to continue to evaluate, measure, and refine that process over time. By using this process, you’ll always have a benchmark against which to measure your results.
When you're ready to get started, learn how to map out processes within Six Sigma.
Check out our guideWhat is Lean Six Sigma?
Some multifaceted business problems require a multifaceted problem-solving approach. In cases where businesses need to both eliminate waste and improve processes, they turn to a hybrid methodology that combines Lean and Six Sigma.
A Lean approach to Six Sigma problem solving can accelerate results and improves processes more quickly and efficiently. A common misconception of the hybrid Lean Six Sigma is that it’s too complex or intended only for Fortune 500 companies; however, with the right implementation, Lean Six Sigma can ensure any organization sees immediate quality and output improvements.
Let’s take a quick look at some of the benefits that Lean Six Sigma will bring to your team.
In with the good; out with the bad
Ultimately, combining the principles found in Lean and Six Sigma solves many of the pitfalls each system has while also amplifying the positive outcomes. For example, a common complaint with Lean is that it’s too focused on the present, making it extremely difficult to shift strategy or forecast. Six Sigma can solve this problem with its focus on data and statistical analysis, which allows for real-time monitoring.
Improve speed and increase quality—at the same time
Companies who implement a Lean and Six Sigma approach in tandem reap the ultimate benefits at the same time. While some companies might think it’s too complicated to train employees on two processes, when done correctly, these companies can quickly see valuable process gains.
Determining the benefits of Lean vs. Sigma may initially reveal one approach as a better fit for your specific business. However, it’s important to consider that in today’s market, customers demand both quickness and quality. Combining Lean Six Sigma gets you both faster.
Use in any industry—and any organization
Their origins are in manufacturing, but the principles of Lean and Six Sigma can apply remarkably well to any business, primarily when planned and implemented as Lean Six Sigma. Companies from hospitals to big-box retailers have used Lean Six Sigma to accomplish their goals operationally in improving processes and removing waste in any repeatable process.
By leveraging the speed strengths of Lean and the data-driven quality strengths of Six Sigma, any organization in any industry will see significant value that impacts both cost and satisfaction.
As with any new process or system implementation, the key to success is preparing the team properly and ensuring a roadmap for continued adoption. One of the most significant barriers to successful implementation is consistency. Whether you choose to implement Lean, Six Sigma, or the combined Lean Six Sigma, your team will see optimum value with a way to track that consistency and innovation.
About Lucidchart
Lucidchart, a cloud-based intelligent diagramming application, is a core component of Lucid Software's Visual Collaboration Suite. This intuitive, cloud-based solution empowers teams to collaborate in real-time to build flowcharts, mockups, UML diagrams, customer journey maps, and more. Lucidchart propels teams forward to build the future faster. Lucid is proud to serve top businesses around the world, including customers such as Google, GE, and NBC Universal, and 99% of the Fortune 500. Lucid partners with industry leaders, including Google, Atlassian, and Microsoft. Since its founding, Lucid has received numerous awards for its products, business, and workplace culture. For more information, visit lucidchart.com.
Related articles
Limitations of Six Sigma Steps and What to Do About Them
Learn how to follow the Six Sigma steps, where the limitations of the methodology lie, and what methodologies you may want to use instead.
5 Lean Six Sigma principles you should adopt immediately
Combine two of the most prominent project management methodologies, and what do you get? Lean Six Sigma. Learn more about the method that can both eliminate waste and reduce defects in your company's workflow.