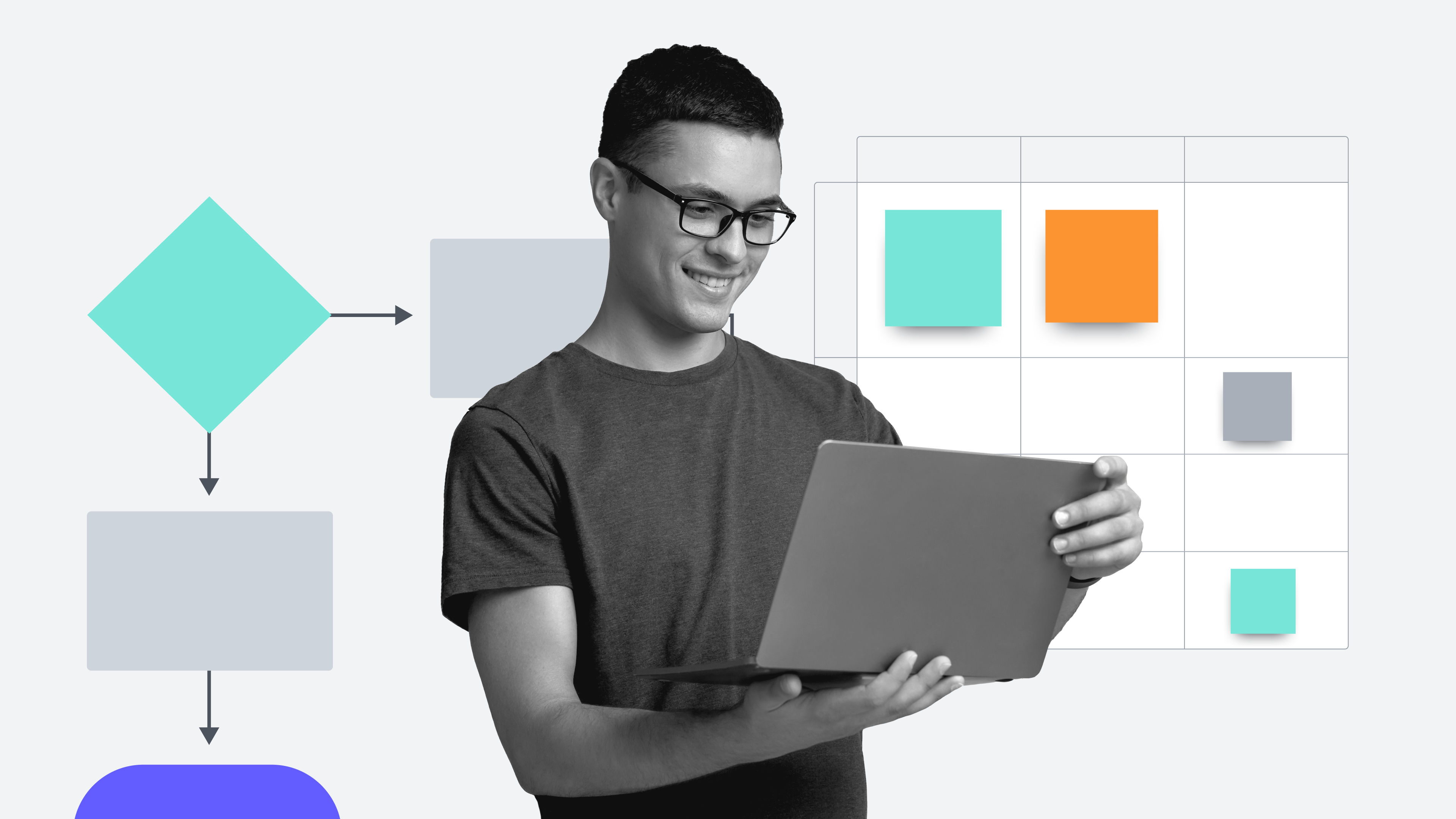
Why you need the Lean PDCA cycle to improve your iterative process
Reading time: about 6 min
Topics:
If your organization uses Lean methodology, you’re focused on building only what your customers want without wasting any time or resources to get the job done. And the most important tool you have to do this properly is the Plan-Do-Check-Act (PDCA) cycle.
The PDCA cycle, also known as the four-stage iterative approach, is a tool to refine an iterative process so that it becomes better and better over time. While PDCA cycles are most common in product development and engineering, you can still use them in other fields—just about every job has repetitive processes that you can improve, from marketing to sales to human resources.
Keep reading to learn more about iterative processes, why the PDCA cycle is important to improve them, and how each step of the PDCA cycle helps you create better products with less waste during each iteration.
What is an iterative process?
In a non-iterative process, you plan out each phase of your project in advance, and the next step cannot come until the current one is complete because future work will build on the work you’re doing now. For example, if you’re going to knit a sweater, you must do it one step at a time, in order: You have to select your pattern and yarn, then knit each piece. You can’t skip ahead and attach the sleeves before you’ve knit the shoulders that the sleeves will attach to.
Iterative processes, however, are based on testing out new ways to do the same thing so that you continuously improve your process as you work towards your goal. Iterative processes are based on trial and error.
For example, while knitting a sweater would be a non-iterative process, designing one would be an iterative process: You would have to test out multiple types of yarn and stitch techniques, and you’d have to knit multiple prototypes until you find what works best.
Iterative processes can be more efficient and adaptable than non-iterative ones. Instead of spending lots of time planning and building specs at the beginning of the project, you start trying things to find what works, adapting to new information, getting feedback, and solving problems as you go. You can also work on multiple elements of your project at the same time since each piece isn’t dependent on the piece before it, which shortens your timeline.
However, iterative processes can risk scope creep. If you’re not investing serious thought at the beginning to define the scope of your project, you could end up getting distracted by side issues that pop up as you’re completing your work.
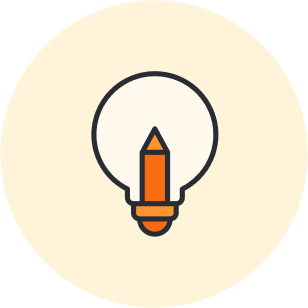
Learn how to create an effective project scope.
Read nowTeams working iteratively also have to cope with vague timelines. Since they aren’t spending a lot of time planning at the beginning of the project, they can’t build very detailed timelines that they have confidence they’ll be able to stick with. Instead, they figure out what works as they go, which may mean that the timeline for when the work will be done is hard to pin down.
Why is the Lean PDCA cycle important to the iterative process?
If your organization uses Lean methodology, you’re focused on reducing waste at every step of your process. Lean methodology is all about using only the truly necessary resources and time to create great products.
The PDCA cycle is how you get there. W. Edwards Deming created this model (it’s also known as the Deming Wheel or Deming Cycle) in the 1950s based on the scientific method. Essentially, you make a hypothesis (i.e., propose a change that could be beneficial), experiment with it, measure the results, and then decide how to proceed.
If you work through the steps of the PDCA cycle multiple times, you should find better and better ways to produce your work. In the long run, you’ll do a better job with fewer resources, creating more efficiency, less waste, and a higher-quality product.
The iterative four-stage approach of the PDCA cycle
PDCA stands for Plan, Do, Check, Act. Less commonly, you’ll see it written as PDSA, with S for Study.
Here are the basic steps of the PDCA cycle:
Plan
During this phase, you find either a problem that you want to solve or an opportunity for improvement you want to seize. You plan out the change you want to make to your process to improve it.
Do
Next, you need to try out your change. Find a way to implement it—but don’t go overboard. Lean development for iterative processes is not about changing everything all at once, which would be a recipe for chaos instead of a way to reduce waste.
Instead, you need to choose small improvements that you can test out in controlled ways so that you don’t break your entire process. For example, try implementing your proposed change on just one team so you can see how it goes.
Check
This is where you examine the results of your experiment. Analyze how the change went. Did it actually solve the problem that you set out to solve? Did it cause other problems you didn’t expect? How could you do it better if you tried the experiment again?
Act
Once you have your findings in hand, you need to decide what to do with them. If your experiment was a success, then you can make it the standard for your process going forward—and congratulations on improving your process for its next iteration! However, if the change caused more problems than it solved, you can decide to shelve it and try something else next time.
The PDCA cycle is not something you’re going to do just once. Even if your change was a smashing success, you’ll need to go through the cycle again with another proposed change later. And if you got poor or mixed results, use what you learned to go back to the drawing board and start again.
As you work through the PDCA cycle, you’ll need something to help you keep track of what you’re planning and learning. Use Lucidchart’s PDCA template. You can document your thoughts and actions for each stage of the cycle so that you have a record of everything you proposed or tried, and you’ll be able to keep track of what your findings and decisions were.
This way, your hard work won’t get lost down the road. You’ll be able to see what you considered, what you decided, what your reasons were, and what you learned. That will help you decide what your next steps are, and you’ll have detailed notes to review next time you need to start a PDCA cycle so you don’t replicate work.
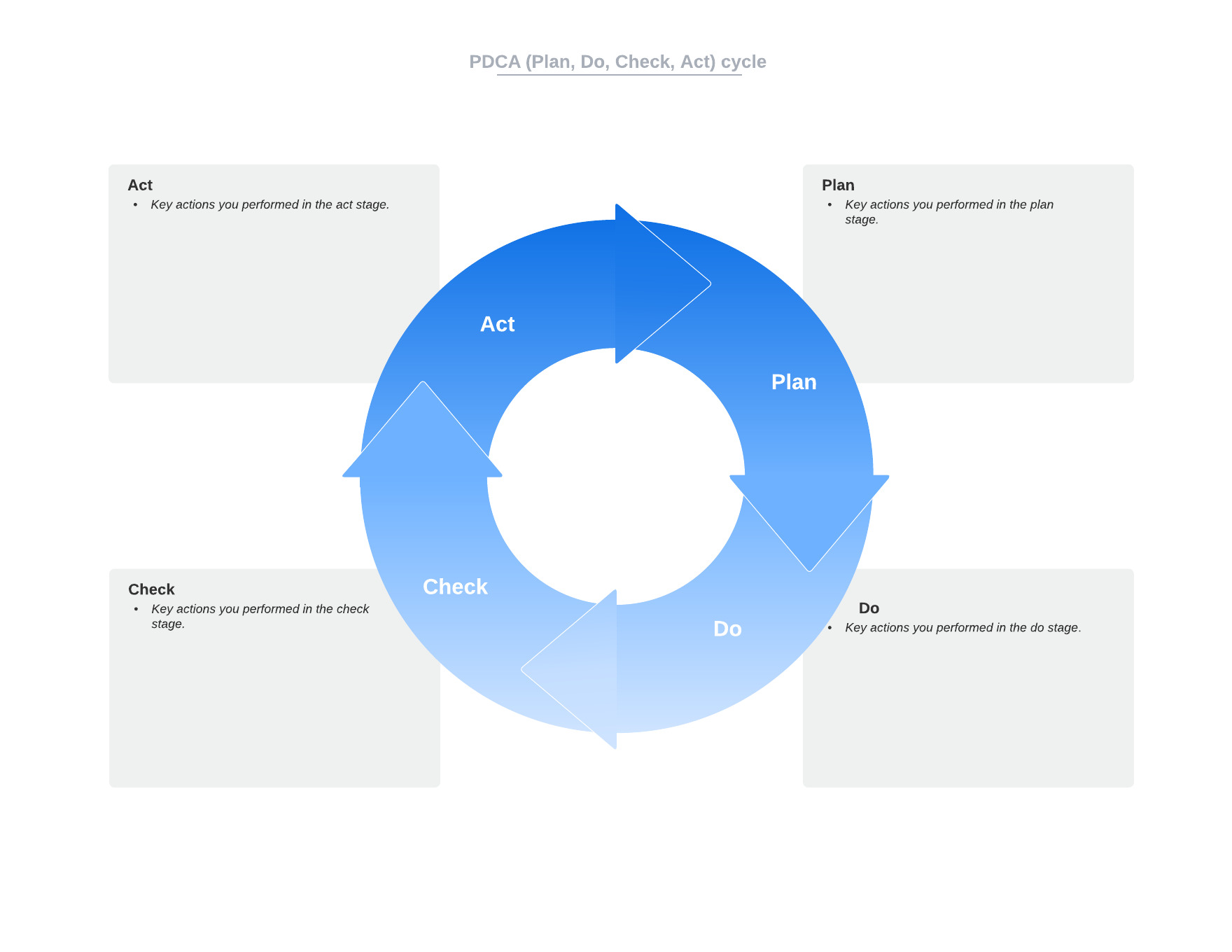
Use the PDCA cycle to improve your iterations
If you’re using Lean methodology to get the most out of your iterative processes, you need to get familiar with the PDCA cycle. Go through the steps each time you need to make an improvement to your process, and your team will get better and better over time. In the end, you’ll produce better work faster and with fewer resources, which eliminates waste and gets your customers exactly what they’re looking for.
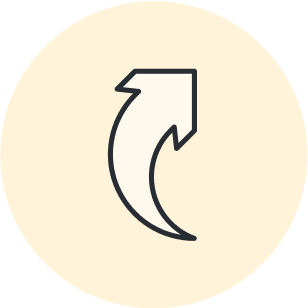
Ready to begin the PDCA iterative process? Use our free template!
Try for freeAbout Lucidchart
Lucidchart, a cloud-based intelligent diagramming application, is a core component of Lucid Software's Visual Collaboration Suite. This intuitive, cloud-based solution empowers teams to collaborate in real-time to build flowcharts, mockups, UML diagrams, customer journey maps, and more. Lucidchart propels teams forward to build the future faster. Lucid is proud to serve top businesses around the world, including customers such as Google, GE, and NBC Universal, and 99% of the Fortune 500. Lucid partners with industry leaders, including Google, Atlassian, and Microsoft. Since its founding, Lucid has received numerous awards for its products, business, and workplace culture. For more information, visit lucidchart.com.
Related articles
Why you must continuously evaluate and improve business processes
As businesses scale and try to innovate to keep up with the competition, the need to evaluate current practices and improve processes becomes inevitable. Learn more about why process improvement is essential.
How to (really) improve process efficiency
To lower production costs and increase profits, you need to evaluate and continually optimize the processes within your company to make them as efficient as possible. In this article, we'll explain how to measure and improve process efficiency.
How to avoid scope creep (and the circumstances that lead to it)
Use these tips to prevent too many unexpected additions or changes from creeping into your projects.
How to apply the Plan-Do-Check-Act (PDCA) model to improve your business
The Plan-Do-Check-Act cycle helps teams transition to a culture of continuous improvement. Learn how the cycle works and how to implement it.