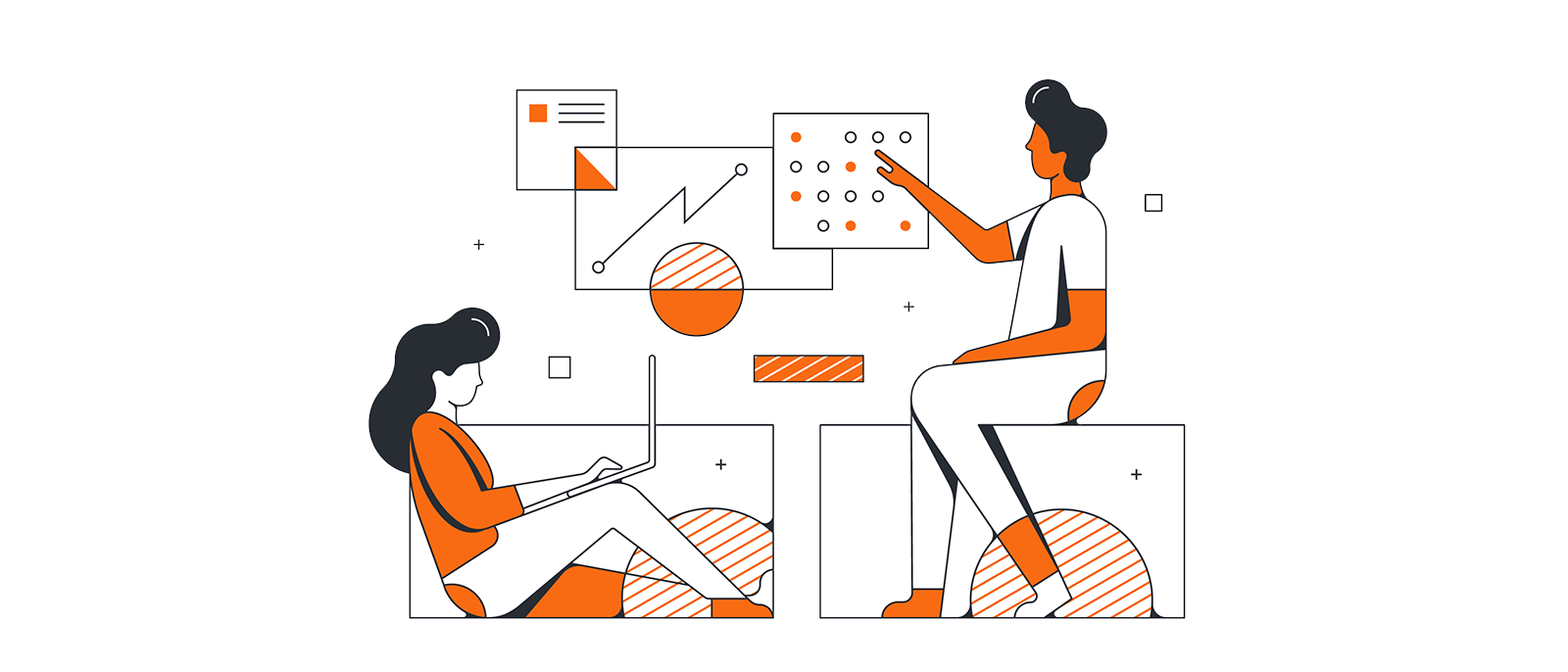
All about inventory management
Lucid Content
Reading time: about 6 min
So you’ve decided to sell your products. That’s great! Now comes one of the hard parts: keeping track of what you’re selling. After all, it may not be difficult to handle selling, say, fifty belts. But when it comes to managing fifty thousand belts, suddenly things become a lot more intense.
This is where inventory management comes in. Thanks to the advent of automation and modern inventory software, there are more options than ever before. That’s great for your business, but can initially feel overwhelming. Here’s your guide to the fundamentals of inventory management so you can feel more confident about getting started.
What is inventory management?
Inventory management is the process of keeping track of the items in your warehouse. It involves knowing how much you have of a certain product and also how much you need. This is important because you don’t want inventory that’s not selling taking up valuable space in your warehouse; that costs money and could also lead to products expiring before they’re sold. On the other hand, not having enough inventory in your warehouse means you’ll lose out on valuable sales and may also upset customers who are wishing to buy your products. In short, you want the right amount of items and the right kind of items in the right place at the right times.
Here are some important inventory management terms and definitions to know:
SKU–This stands for “stock keeping unit” and is a code that is assigned to each specific type of product. If you carry fifty different types of hair brushes, you’ll have fifty different SKUs.
Carrying cost–This is how much it costs the company to keep inventory on hand. Sometimes this is referred to as the “holding cost” or “inventory cost.”
Cycle counting–This is an audit of products in stock in a warehouse. Unlike an audit, this is performed every day or week.
Costing method–The way a product’s retail price is determined.
Lead time–The time between when an item is ordered and when it arrives to your inventory warehouse.
Why is inventory management important?
Having inventory carries a certain amount of risk. It costs money to keep each item safe and stored properly and the longer a product sits in a warehouse, the more it ends up costing your business in the long run. There’s also the potential that consumer demand could change as your product is stored.
Take phone dangles, for example. They were in high demand until cell phone manufacturers obliterated headphone jacks. Woe to the business that kept a hefty stockpile of phone dangles sitting in a warehouse waiting to be sold—they would have had to absorb the cost of those obsolete dangles just as soon as customer demand plummeted.
Proper inventory management means mitigating the cost of storing items while also keeping plenty of items on hand so revenue can be gained from their sale. Most companies have automated their inventory management. Software automatically determines when to reorder items from the manufacturer based on the remaining levels of stock and current rate of sale.
Some small businesses manage their inventory manually, but medium, large, and enterprise businesses have such massive inventory that a manual counting would be impossible. Imagine if Amazon tried keeping track of its inventory manually!
Types of inventory management
Perpetual–Perpetual inventory management is constantly updated. When an item is sold, the system updates, so the business has the most up-to-date picture of its inventory at any given time. Perpetual inventory management requires automation and specialized software that requires deployment, management, maintenance, and regular updating.
Perpetual inventory management is a necessity in most online businesses because many people will often try to purchase the same item at once. For instance, if Anthropologie has 25 purple jumpsuits left, it needs to know down to the second when the jumpsuits are sold out. Otherwise, customers will purchase an item that isn’t in stock.
Periodic–Periodic inventory management relies on physical counts of products during a set duration of time, such as every week or every day. This type of system relies on manual audits and it can be difficult to pinpoint discrepancies because there’s a larger amount of time between inventory counts. However, periodic inventory management systems are less expensive to run than perpetual inventory management systems.
Barcode–A barcode inventory system combines automation with manual labor. In this form of inventory management, an employee scans each item in the inventory with a barcode scanner. That information is reported to the inventory management software. Barcode scanning eliminates many of the errors that come from manual counting.
RFID inventory systems–RFID tags are similar to barcodes, but they include more information. RFID tags don’t require a line of sight like barcodes do, which means gathering inventory information is a matter of waving an RFID wand over the area of inventory and obtaining accurate information. The drawback is that an RFID system is very expensive and is normally only used for higher-value items like televisions and sporting equipment.
Inventory management techniques
There are several different inventory management methods and each is helpful for developing inventory management best practices.
Setting par levels–Par levels are the bare minimum amount of inventory you should have on hand. As soon as inventory hits below your predetermined par level, an order is automatically placed to bring inventory up to par. To determine your par levels, you’ll need to use data from purchases so you know how much inventory should be kept on hand.
FIFO (First-In-First-Out)–The FIFO method is similar to grabbing a jug of milk from the fridge at the grocery store: the jug you grab at the front of the row is the oldest milk. It was placed in the fridge before the rest of the milk and should, therefore, be sold first. Your oldest inventory should be sold first to accurately reflect the cost of inventory and to avoid spoilage and waste.
Audits–This is basically just a fancy way of saying “counting.” An inventory audit is a thorough counting of each item in inventory. This helps your business understand what’s being sold for better inventory forecasting.
Forecasting–Forecasting allows businesses to predict when they’ll need to place an order based on trends and base demands. This ensures there isn’t a gap between the time an item runs out and the time that item is restocked.
ABC management–This is a technique used to classify inventory, ranking items on how important they are to your business. “A” items are of greatest importance. “B” items are of less importance and “C” items are of the least importance.
JIT (Just in time)–This type of inventory management places greatest importance on minimizing waste and increasing efficiency. Raw goods are ordered from the manufacturer only when they’re needed for the production process, so very little is kept on hand for inventory. Car manufacturers like Toyota use this technique to make sure they only keep enough parts in stock for the amount of cars they’re predicted to produce.
Inventory management can streamline the way you bring products to customers. Don’t be afraid to try a process or solution out. If it doesn’t work for your business, you can try a different system. But one thing is for sure: when you have control over your inventory, it ripples throughout your organization.
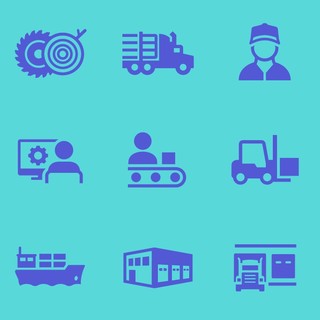
Learn more about the Theory of Constraints and see what tools you can use to optimize your processes
Learn moreAbout Lucidchart
Lucidchart, a cloud-based intelligent diagramming application, is a core component of Lucid Software's Visual Collaboration Suite. This intuitive, cloud-based solution empowers teams to collaborate in real-time to build flowcharts, mockups, UML diagrams, customer journey maps, and more. Lucidchart propels teams forward to build the future faster. Lucid is proud to serve top businesses around the world, including customers such as Google, GE, and NBC Universal, and 99% of the Fortune 500. Lucid partners with industry leaders, including Google, Atlassian, and Microsoft. Since its founding, Lucid has received numerous awards for its products, business, and workplace culture. For more information, visit lucidchart.com.