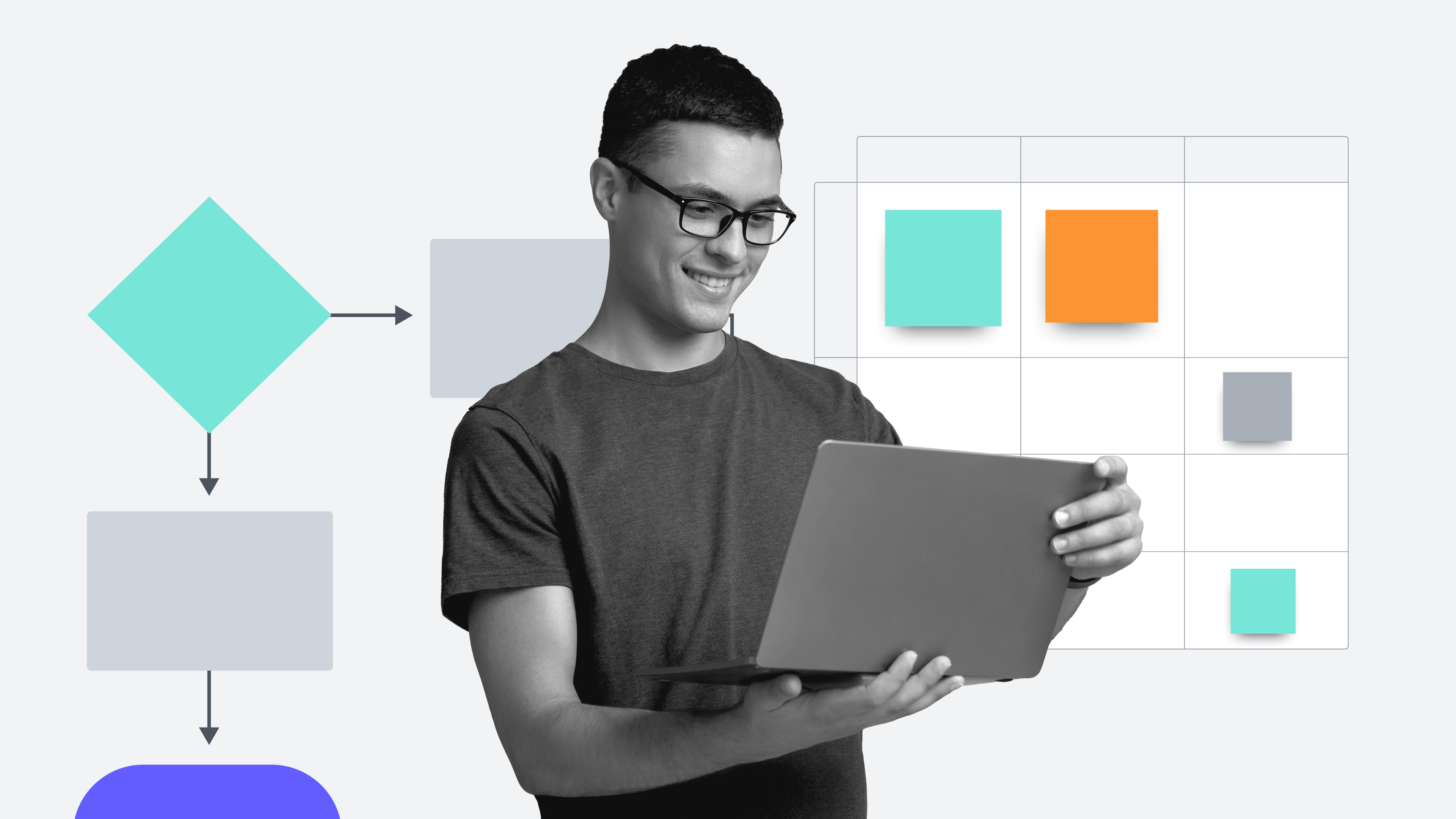
Tout savoir sur les 5S en Lean Manufacturing
Temps de lecture : environ 8 min
Sujets :
Il y a de fortes chances que vous ayez assemblé de nombreux meubles achetés dans le commerce. Vous avez probablement mis au point une méthode pour vous assurer, par exemple, que votre bibliothèque reste une bibliothèque. La fabrication à plus grande échelle n’est pas très différente : il existe des méthodes pour s’assurer que les bibliothèques finissent par être des bibliothèques et que les voitures finissent par être des voitures, avec le moins de gaspillage possible, et une qualité et une efficacité optimales.
L’une de ces méthodes est le système des 5S, développé dans le cadre du Lean Manufacturing et de la théorie des contraintes (TOC). Au sein de cette dernière, la méthode des 5S permet d’exploiter les contraintes.
Un aperçu pratique de la méthode 5S et de la manière dont vous pouvez l’utiliser pour améliorer votre processus de production Lean.
Qu’est-ce que la méthode 5S ?
La méthode des 5S vise à garantir la sécurité, l’organisation et l’efficacité du lieu de travail. Bien que l’on attribue son développement à l’équipe japonaise de Toyota, le concept original a été mis au point par Ford qui l’avait appelé CANDO pour Cleaning Up, Arranging, Neatness, Discipline, et Ongoing Improvement (nettoyage, rangement, propreté, discipline et amélioration continue).
Lorsque l’équipe de Toyota a visité l’usine de Ford, elle a rapporté avec elle la méthode CANDO et les techniques révolutionnaires de la chaîne de montage du constructeur. La marque japonaise a ensuite repris ces principes pour créer la technique des 5S.
Bien que cette technique soit à l’origine destinée à la production automobile, elle peut facilement être adaptée à d’autres secteurs non industriels, notamment la technologie, les soins de santé et l’administration publique.
À quoi correspondent les 5S ?
Les 5S étaient à l’origine des mots japonais (Seiri, Seiton, Seiso, Seiketsu et Shitsuke). Ils ont depuis été traduits en anglais tout en conservant leur signification originale. Aujourd’hui, les 5S signifient :
- Sort (trier) : débarrassez-vous des matériaux inutiles et séparez vos outils, vos pièces et vos instructions.
- Set in order (mettre en ordre) : rangez les outils et les pièces dans l’ordre dans lequel ils seront nécessaires.
- Shine (faire briller) : nettoyez !
- Standardize (normaliser) : intégrer le nettoyage dans les tâches quotidiennes.
- Sustain (maintenir) : faites des 5S une démarche permanente en vous assurant que les quatre premiers S deviennent une habitude.
Il existe également un sixième S. Étant donné que l’un des principaux avantages des 5S est l’élimination du gaspillage, son ajout est tout à fait logique :
- Sécurité : organisez votre lieu de travail pour optimiser la sécurité.
Avantages de la méthode 5S Lean
Rappelez-vous les fois où vous avez monté des meubles. Vous avez probablement suivi naturellement la technique des 5S ci-dessus pour ne pas perdre de temps ni de ressources. Les avantages des 5S dans le cadre de la production Lean sont similaires :
- Coût inférieur : moins de gaspillage de main d’œuvre et de matériaux signifie une diminution des coûts.
- Sécurité accrue : qu’il s’agisse d’utiliser les 6S ou de sécuriser chaque étape, l’accent mis sur la sécurité se traduit par un meilleur environnement de travail.
- Disponibilité des équipements : si les travailleurs accumulent du matériel parce qu’ils ne sont pas sûrs de ce dont ils auront besoin, l’efficacité s’en trouve réduite à tous les niveaux. Le système des 5S vise à n’utiliser que ce qui est nécessaire.
- Vitesse accrue : avec tous les équipements et matériaux nécessaires à portée de main, les travailleurs peuvent se concentrer sur l’assemblage.
- Moins de frustration : les travailleurs se sentent plus motivés lorsqu’ils accomplissent des tâches sans être contrariés par des obstacles.
Comment les 5S s’intègrent au Lean Manufacturing
L’approche des 5S s’associe parfaitement au Lean Manufacturing, car les principes du Lean mettent l’accent sur la gestion du gaspillage, quand le modèle des 5S insiste sur la propreté et l’organisation de l’espace de travail. Après tout, un environnement bien ordonné se traduit par une plus grande sécurité sur le lieu de travail, ainsi que des tâches réalisées plus rapidement et de manière plus stratégique.
La méthode des 5S complète également d’autres éléments du Lean Manufacturing. Par exemple, il est beaucoup plus facile de mettre en œuvre le système Kanban dans un lieu de travail organisé et sûr. De plus, lorsque tout est en ordre grâce aux 5S, il est plus facile d’identifier les problèmes et les obstacles avant qu’ils ne deviennent des enjeux majeurs.
Comment réussir la mise en œuvre des 5S en Lean
La technique des 5S semble simple sur le papier, mais elle est souvent difficile à mettre en œuvre. Après tout, il est déjà difficile de nettoyer et d’organiser une salle de bains : imaginez faire de même pour l’ensemble d’une usine. Voici quelques étapes importantes pour y parvenir efficacement :
1. Promouvoir la méthode 5S
Bien qu’il soit tentant de laisser les principes des 5S aux gestionnaires, cette technique ne fonctionne réellement que si tout le monde y adhère. Lorsque l’ensemble du personnel s’investit dans le programme, la probabilité de respecter les différents aspects augmente de façon exponentielle.
Bien qu’une mise en œuvre réussie des 5S nécessite la participation de tous, vous pouvez choisir d’avoir des spécialistes qui supervisent les efforts dans ce domaine. Ces coordinateurs peuvent récompenser les employés qui appliquent les principes des 5S et initier les nouvelles recrues au programme. Ce faisant, ils contribuent à maintenir l’élan d’une nouvelle stratégie des 5S.
2. Mettre en place une formation 5S
L’avantage des 5S est qu’ils sont relativement intuitifs, de sorte que la formation n’a pas besoin de durer des mois. Elle peut se dérouler en petits groupes ou dans le cadre d’une grande session générale au sein de l’entreprise. Elle peut également être dispensée individuellement en ligne à l’aide de tutoriels vidéo. Quel que soit le mode de formation choisi par votre organisation, veillez à la personnaliser en fonction des stations de travail qui seront réellement utilisées. Il ne servirait pas à grand-chose de former votre personnel à la chaîne de montage d’une autre entreprise.
3. Créer des signaux visuels
Il est temps de sortir le pistolet d’étiquetage. Dans un espace de travail organisé, tout est étiqueté et rangé à sa place. Toyota utilise même un système d’« étiquettes rouges » qui identifient les objets et les matériaux qui peuvent être considérés comme du gaspillage afin de déterminer ce qu’il faut en faire (les jeter, les déplacer, etc.).
Les repères visuels sont essentiels pour la partie « tri » des 5S, mais il est important que tous les membres de votre organisation utilisent la même terminologie et le même système d’étiquetage. Parmi les autres repères visuels importants, on retrouve les marquages au sol, les shadow boards, les enseignes et les étiquettes. Ces indices visuels sont utiles à tous les niveaux, qu’il s’agisse de la sécurité, de l’organisation ou de l’efficacité.
4. Écouter
Les meilleures idées pour la mise en œuvre des 5S viendront probablement des personnes qui utilisent le système au quotidien. Écoutez vos employés et envisagez sérieusement d’appliquer leurs suggestions. Encouragez un dialogue ouvert et proposez éventuellement des primes à vos collaborateurs pour les inciter à chercher des améliorations. Faire du processus des 5S un travail d’équipe est essentiel pour réussir sa mise en œuvre dans le cadre du Lean Manufacturing.
Outils et exemples de la méthode 5S
Les 5S peuvent être appliqués à n’importe quel environnement de travail et dans tout type de secteur. Tout ce dont vous avez besoin pour adapter le processus à votre activité, ce sont des bons outils. Si vous travaillez, par exemple, dans le secteur de la santé, les 5S seraient parfaits pour assurer le bon fonctionnement d’une salle d’urgence ou d’une salle d’opération (imaginez que vous vous prépariez à une intervention chirurgicale sans avoir vérifié au préalable que vous disposez de tous les instruments nécessaires).
Voici quelques outils pour vous aider à tirer le meilleur parti de votre stratégie 5S :
Roue de Deming : la roue de Deming (PDCA) est un excellent outil à utiliser pour mettre en œuvre de manière systématique le processus des 5S. Il permet de contrôler la qualité et de s’assurer que vous exercez votre esprit critique dans le cadre de la gestion des processus.
Listes de contrôle : les 5S étant axés sur l’organisation, les listes de contrôle constituent d’excellents outils. Les listes d’audit vous aident à suivre les améliorations mises en œuvre et les domaines qui doivent encore être améliorés. Celles relatives à l’entretien préventif permettent de s’assurer que les travaux de maintenance sont effectués en temps opportun.
Graphiques de tendances : ils suivent l’évolution des résultats, des processus et d’autres données au fil du temps. Vous pourrez ainsi repérer les points à améliorer.
Imprimantes : le système des 5S repose sur la signalisation. Donnez à vos responsables la possibilité d’imprimer leurs propres panneaux à l’aide d’imprimantes grand format.
Machines à étiqueter : étiquetez tout. Soyez sans limites. Disposer de machines à étiqueter permet à chaque pièce d’équipement d’avoir un nom et une place attitrée.
Tableaux de bord : les tableaux de bord facilitent l’application des principes des 5S à votre secteur d’activité. Cette méthode étant axée sur les aspects visuels, les tableaux de bord sont essentiels. Consultez nos modèles et commencez à les adapter à vos besoins.
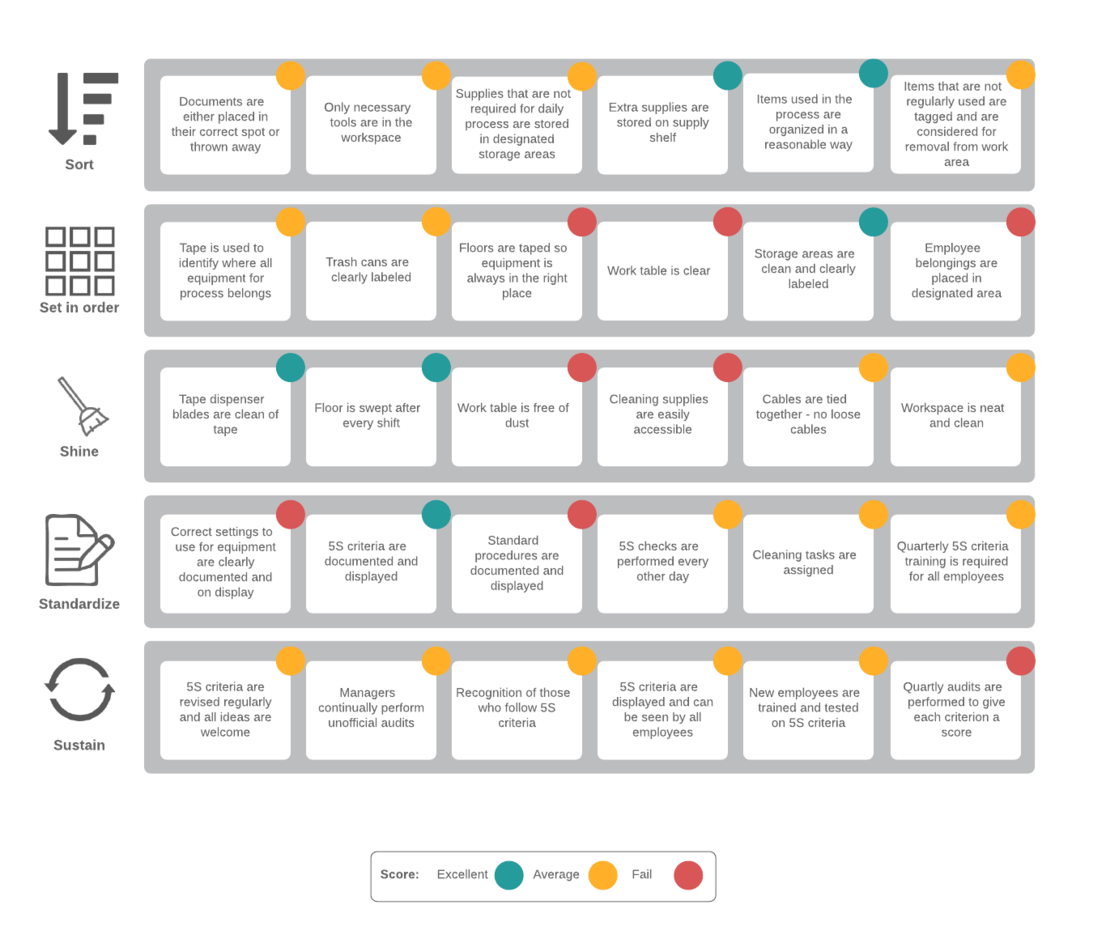
En triant, en remettant les choses dans l’ordre, en veillant à ce que tout soit propre et bien entretenu, en normalisant les processus, en respectant les bonnes pratiques et en gardant à l’esprit la sécurité des employés, vous réduirez le gaspillage, augmenterez l’efficacité et veillerez à ce que tous les systèmes fonctionnent de manière optimale.
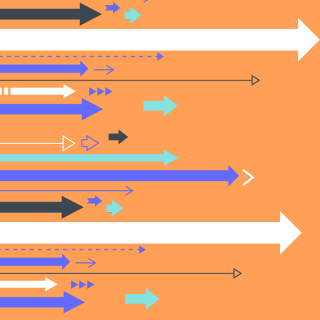
Découvrez comment Lucidchart peut vous aider à améliorer et à étendre vos processus métier.
En savoir plusÀ propos de Lucidchart
Lucidchart, une application de création de diagrammes intelligents basée sur le cloud, est un élément central de la suite de collaboration visuelle de Lucid. Cet outil intuitif, basé sur le cloud, permet aux équipes de collaborer en temps réel pour créer des logigrammes, des maquettes, des diagrammes UML, des cartes de parcours client, et bien plus encore. Lucidchart permet aux équipes d'aller de l'avant et de bâtir l'avenir plus rapidement. Lucid est fier de compter parmi ses clients des organisations de premier plan dans le monde entier, telles que Google, GE et NBC Universal, ainsi que 99 % des entreprises figurant au classement Fortune 500. Lucid travaille en partenariat avec les leaders du marché, notamment Google, Atlassian et Microsoft. Depuis sa création, la société a reçu de nombreuses récompenses pour ses produits, son fonctionnement et sa culture d'entreprise. Pour plus d'informations, rendez-vous sur lucidchart.com/fr.